Delta PLC as Modbus TCP Server: A Quick Tutorial
Whether you're managing a small production line or a complex system with multiple Modbus addresses, configuring your Delta PLC as a Modbus TCP server is your first step towards Industrial IoT.
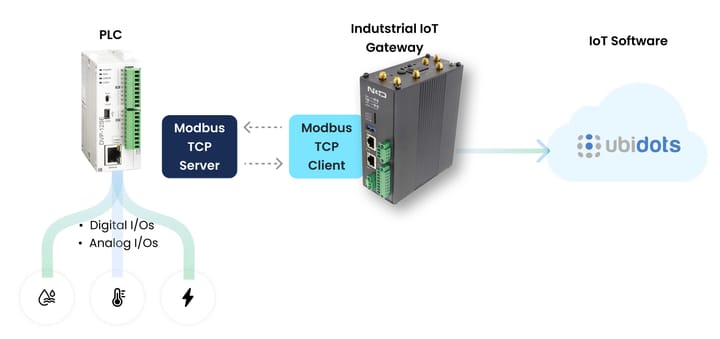
In the intricate world of industrial automation, quality and reliability are non-negotiable. Imagine a factory floor where machines share real-time data and push critical metrics from the PLC to cloud applications for remote monitoring, optimizing processes and reducing downtime. That’s the power of Modbus and IoT. Now, combine it with Delta PLCs—known for their robustness, versatility, and cost-effectiveness—and you have the perfect recipe for streamlined operations. Whether you're managing a small production line or a complex system with multiple Modbus addresses, configuring your Delta PLC as a Modbus TCP server is your first step towards Industrial IoT.
Ready to unlock seamless communication between your Delta PLC and the world of IoT? This tutorial will show you how to configure your PLC as a Modbus TCP server. Let's dive in and bridge the gap between your factory floor and the digital future.
Introduction to Modbus and Delta PLCs
What is Modbus?
Modbus is a communication protocol developed in 1979 by Modicon, now Schneider Electric. It's designed for industrial automation systems, allowing devices to communicate over various types of networks. At its core, Modbus is a master-slave protocol, which means a single device (the master/client) can request information from multiple devices (the slaves/servers). This setup is ideal for monitoring and controlling equipment in real-time.
The protocol is versatile, supporting different transmission modes like Modbus RTU and Modbus TCP. Modbus RTU is used for serial communication, while Modbus TCP leverages Ethernet networks, making it perfect for modern industrial environments. Modbus' simplicity and open nature have made it a popular choice for connecting a wide range of devices, including sensors, actuators, and PLCs, such as the Delta DVP series.
In a world where interoperability is key, the Modbus protocol stands out for its ability to integrate devices from various manufacturers. It uses a simple messaging structure, which makes it easy to implement and troubleshoot. Whether you're dealing with simple data exchanges or complex automation tasks, Modbus ensures seamless communication across your industrial systems.
Why Choose a Delta DVP Series PLC?
Delta DVP PLCs have carved a niche in the automation industry, gaining recognition for their reliability and cost-effectiveness. Emerging as a significant player, Delta Electronics has been around since 1971. The DVP series, in particular, stands out for its versatility and robustness, making it a preferred choice for many industrial applications.
When it comes to cost, Delta DVP PLCs offer an affordable alternative to traditional giants like Siemens or Allen Bradley. While the latter brands are known for their high-quality products, they often come with a hefty price tag. Delta PLCs, on the other hand, provide a more budget-friendly option without compromising on performance. This balance of quality and affordability makes them an attractive choice for businesses looking to optimize their automation processes without breaking the bank.
These compact controllers also come with user-friendly software that simplifies programming, ensuring ease of use even for beginners. Delta offers a range of PLC series, each designed to meet specific automation needs:
- DVP Series: These small and flexible PLCs are ideal for simple to mid-level tasks, providing a perfect balance between functionality and efficiency.
- AS Series: Modular PLCs designed for advanced tasks, including motion control, offering scalability for growing automation demands.
- AH Series: These powerful PLCs are tailored for large and complex systems, equipped with multi-axis motion control capabilities to handle intricate automation challenges.
Modbus-Compatible Delta PLCs
Delta PLCs, especially the DVP series, offer unparalleled reliability and efficiency. They are designed to handle complex automation tasks with ease, thanks to their robust hardware configuration. The DVP-12SE model, for example, is known for its versatility and robustness. This makes it an ideal choice for operations requiring extensive data exchanges.
Here's a comparison table of popular Delta PLC models and their Modbus support:
Model | Modbus RTU Support | Modbus TCP Support | Comments |
DVP12SE | Yes | Yes | Built-in Modbus TCP/IP and EtherNet/IP support. |
DVP28SE | Yes | Yes | Fully supports Modbus TCP/IP communication with dual Ethernet ports. |
DVP-SE2 Series | Yes | Yes | Advanced series with dual Ethernet ports supporting Modbus TCP client/server protocols. |
DVP-ES2-E Series | Yes | Yes | Equipped with Ethernet capabilities supporting Modbus TCP and EtherNet/IP (slave). |
DVP-14SS2 | Yes | No | Can be extended for Modbus TCP support using the DVPEN01-SL Module. |
DVP14SS211R | Yes | No | Requires the DVPEN01-SL Module for Modbus TCP compatibility. |
DVP16SP11R | Yes | No | Can use the DVPEN01-SL Module to enable Modbus TCP. |
DVP-12SA2 | Yes | No | Modbus TCP is possible with the addition of the DVPEN01-SL Module. |
DVP28SV | Yes | Yes | Features built-in Ethernet ports supporting Modbus TCP. |
DVP16SP | Yes | No | Does not support Modbus TCP natively but can be extended with the DVPEN01-SL Module. |
DVP-14SS2 | Yes | No | Compatible with the DVPEN01-SL Module for Modbus TCP functionality. |
The table provides a quick glance at some of the popular Delta PLC models and their compatibility with Modbus protocols. Whether you need TCP or RTU support, Delta has you covered.
Adding Modbus Support With the DVPEN01-SL Module
In the case of the DVP-EH3-L, DVP-MC, DVP-SA2, SE, SV2, SX2 series that may not have Modbus TCP support, check out the DVPEN01-SL module: an essential add-on for enabling Ethernet-based communication. This module is designed specifically for these Delta PLC series, providing seamless integration and expanding their capabilities to include Modbus TCP protocol support.
With the DVPEN01-SL, you can establish up to 32 client connections and 16 server connections, ensuring robust data exchange for complex industrial networks. It features smart RTU mapping, allowing you to bridge serial Modbus RTU devices to Ethernet-based systems effortlessly. Additionally, its simple firewall offers an extra layer of security, protecting your PLC from unauthorized access.
By adding the DVPEN01-SL module, you can unlock the full potential of your Delta PLC, connecting it to modern industrial IoT platforms and ensuring future-proof communication for your automation needs.
This guide covers the configuration and use of Modbus TCP, tailored to the Delta PLC models listed above that are marked as compatible with Modbus TCP, such as the DVP-12SE and DVP28SV. By following the steps outlined, you can ensure seamless integration and efficient data exchange within your industrial network, leveraging the full potential of these robust and versatile Delta PLCs.
Requirements
Hardware Requirements
- DVP-12SE (or any Delta PLC that with Modbus TCP support - see table above)
- Ethernet cable
- Laptop
Software Requirements
- ISPSoft v3.9: Delta's advanced software solution for programming Delta PLCs, supporting multiple languages and complex automation projects, including Modbus TCP/IP capabilities. Download it here.
Note: Delta provides two software options for PLC programming:WPLSoft is tailored for older PLC models such as the DVP series. It features a straightforward interface and supports only Ladder Logic programming.ISPSoft accommodates multiple programming languages (LD, FBD, ST) for modern PLCs, including the DVP, AS, and AH series, offering advanced features for complex and large-scale projects.
In this tutorial, we will use ISPSoft for the DVP SE PLC, as WPLSoft lacks Modbus TCP/IP capabilities.
- COMMGR V1.15: Delta's software tool used for configuring communication settings between Delta PLCs and other devices over Ethernet networks. It is key in setting up Modbus TCP/IP communication, allowing users to define network parameters such as IP addresses and communication ports. Download it here.
Step-by-step Guide
Step 1: Configure COMMGR Driver:
Open COMMGR and click on the "add" button:
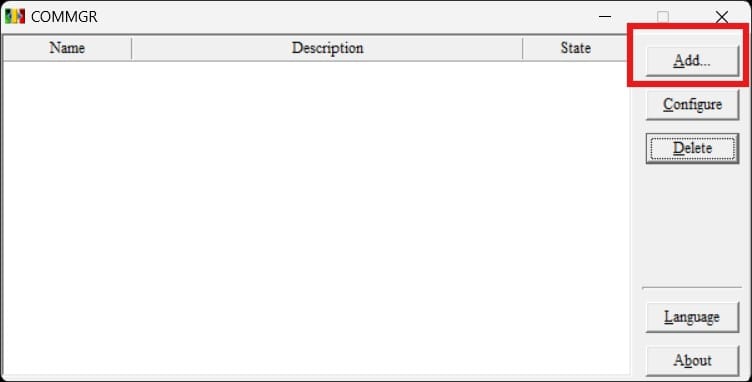
When a new window appears, input the "driver name," choose the "communication setup," and enter the "IP address." Then, click on "OK" to save the driver:
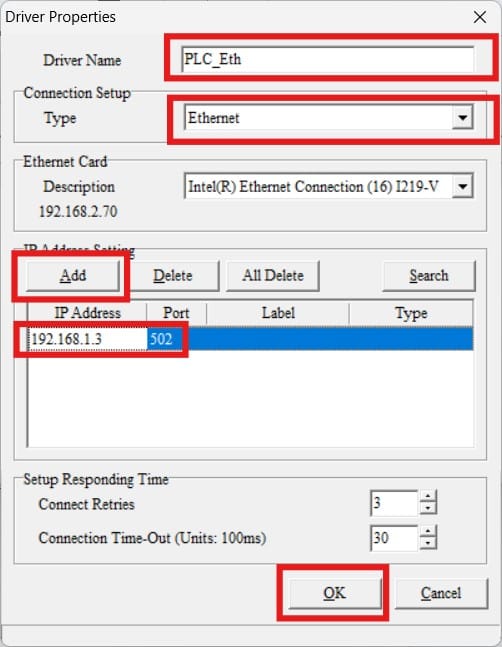
Step 2. Configure ISPSoft Project:
Once you've configured the communication driver in COMMGR, launch ISPSoft. Navigate to the "file" tab and select "new" from the available options.
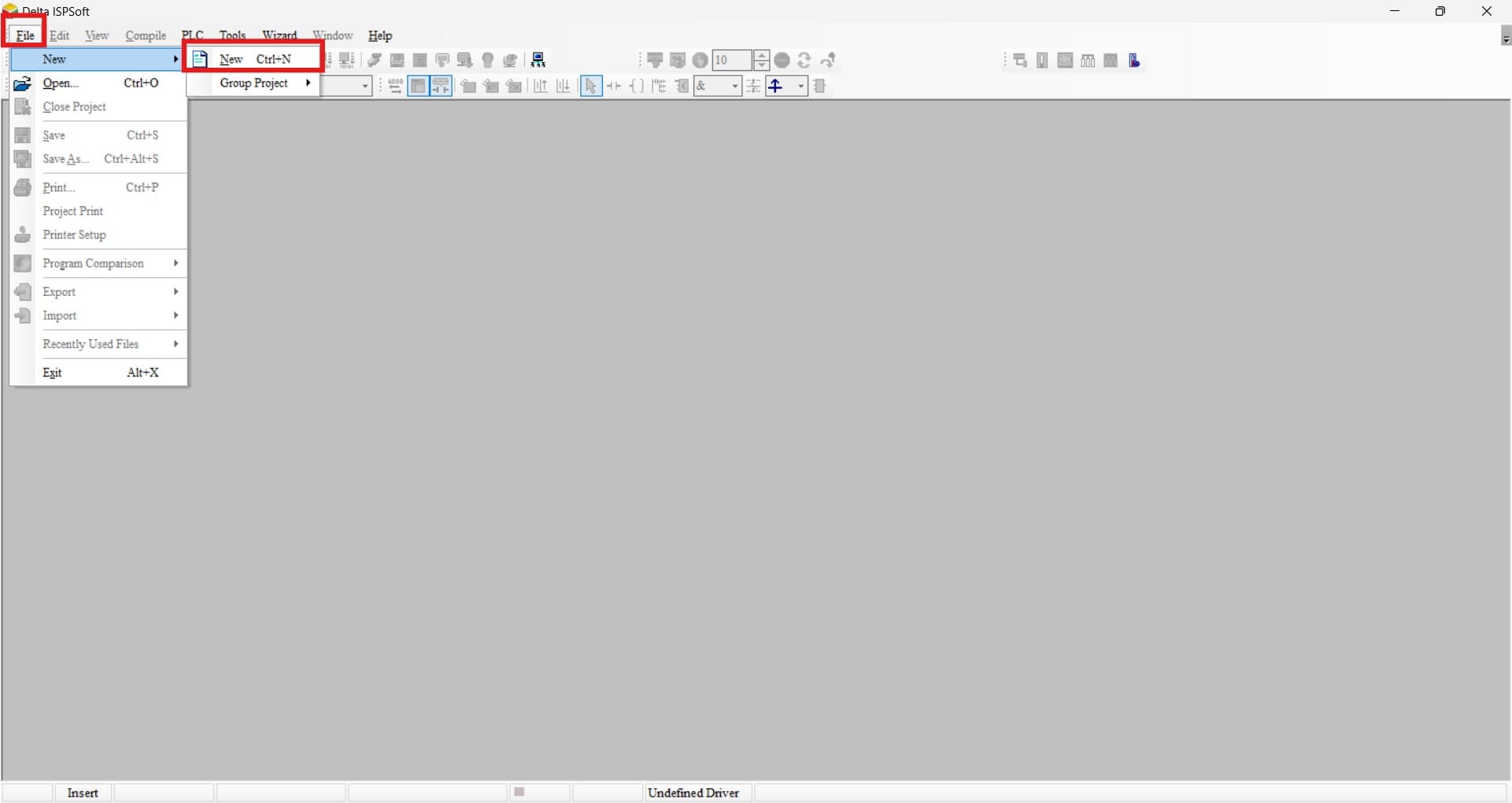
A window will appear. Fill in the necessary details, as seen in the image below, and then click on "OK" to proceed.
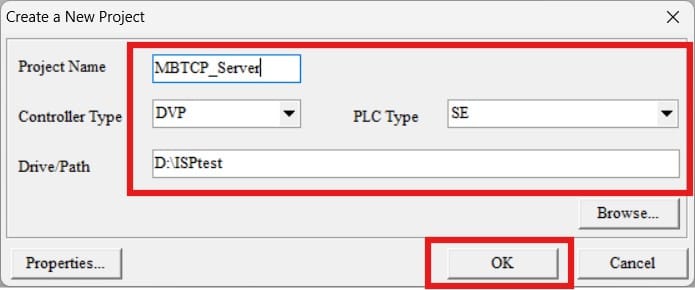
We've successfully initiated our new project. The next step involves adding a POU to program ladder logic for Modbus TCP communication. Follow the steps illustrated in the image below.
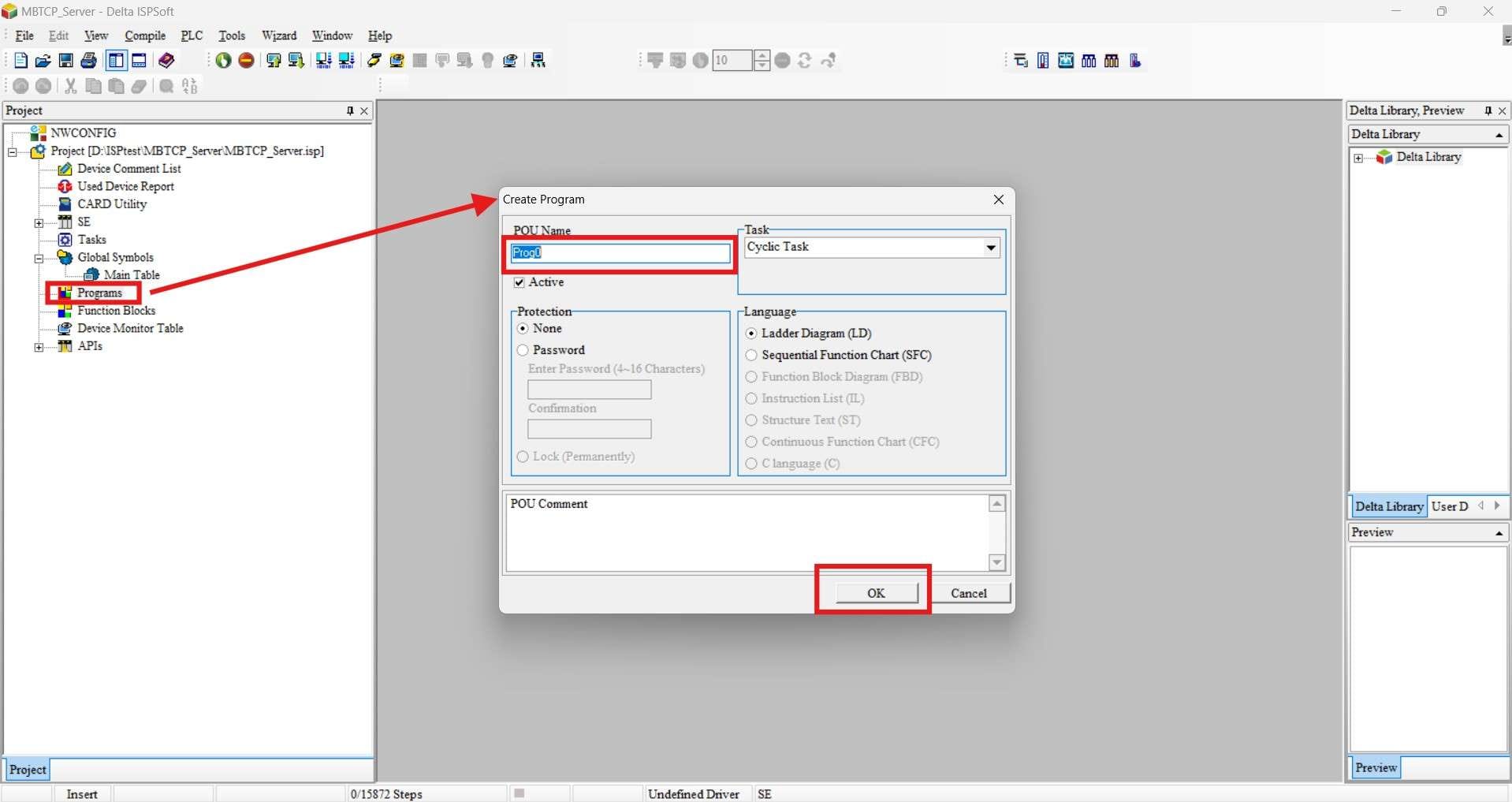
For Modbus TCP communication, the ETHRS API is needed. Begin by navigating to the API section on the left, then click on "communication instruction," and proceed to double click on the "ETHRS" instruction.
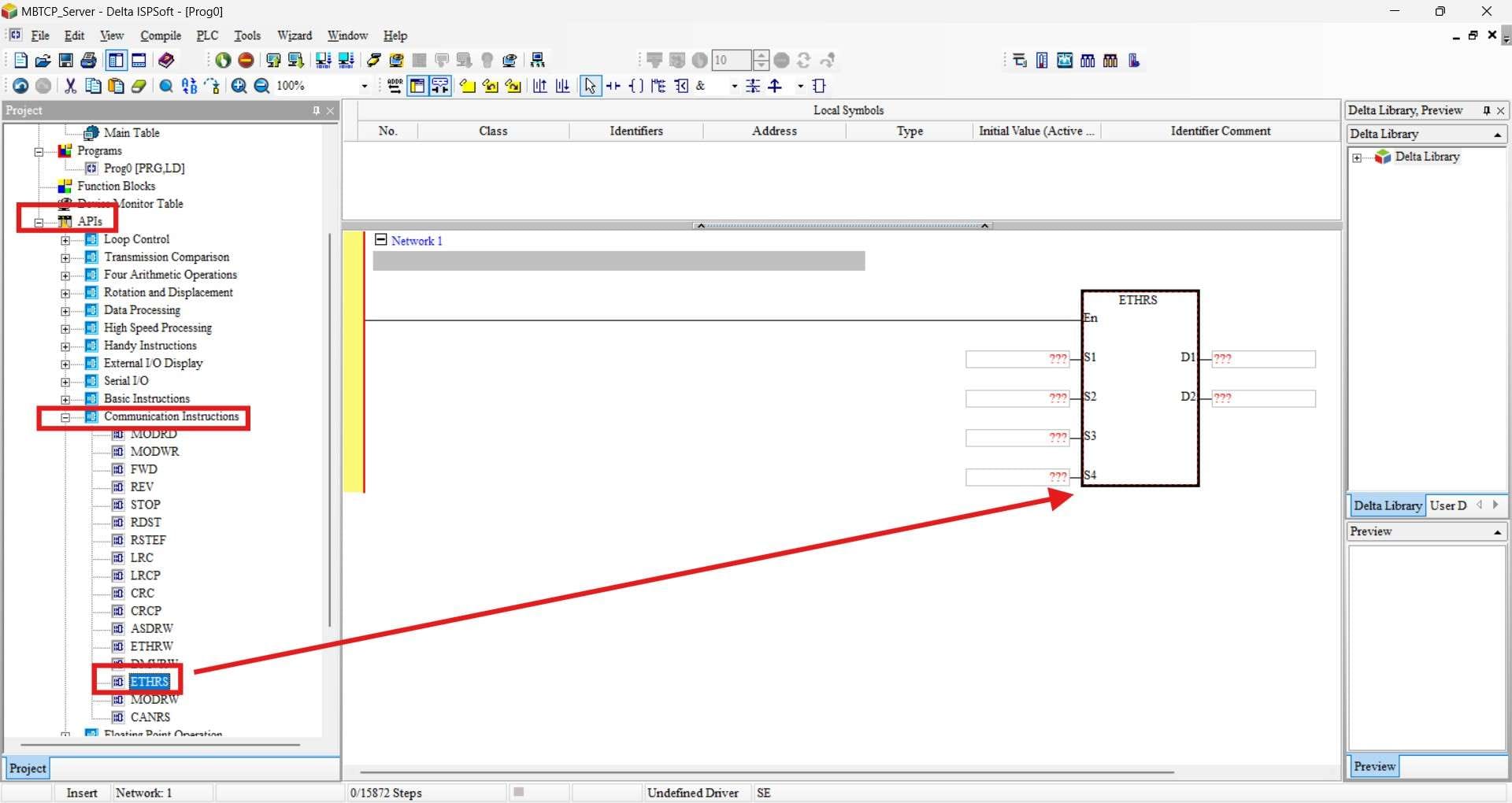
Step 3: Configure the ETHRS Instruction for Modbus TCP Communication
To unlock the full potential of your Delta PLC as a Modbus TCP server, you’ll need to master the ETHRS (Ethernet RS) instruction. Below is a detailed guide on how to set up its operands effectively.
S1: Local and Target Communication Setup
The first operand, S1, defines the local communication port, target IP address, target communication port, and protocol mode.
- Local Communication Port: Assign a value to specify the PLC's Ethernet port. For example, D100 = 10002.
- Target IP Address:
The target device's IP must be split across two registers in hexadecimal format:
If the target IP address is 192.168.1.1, it would be C0A80101 in hexadecimal. Therefore:
D101 = 0101
D102 = C0A8.
- Target Communication Port:
Define the remote device's Ethernet port using D103. Set it to 0 if dynamic assignment is needed.
Important note: Ensure the local and target ports are not identical to avoid conflicts. - Protocol Mode:
Configure the protocol with D104. Assign 1 for TCP (Transmission Control Protocol) or 0 for UDP (User Datagram Protocol). In most Modbus applications, TCP is the preferred choice.
S2: Operating Mode
The second operand, S2, determines whether the PLC functions as a client or a server.
- Assign D105 = 3 to set the PLC in server mode.
- For client operations, use 1 or 2.
The server mode is ideal for responding to Modbus TCP requests from SCADA systems or IoT gateways.
S3 and S4: Data Configuration
These operands define how data is sent and received:
- S3: Specifies the source register for data transmission. For instance, if S3 = D0, the data begins at D0.
- S4: Determines the data length. In some configurations, it might be unnecessary, as in this case, where it is marked invalid.
D1 and D2: Destination and Completion Flag
- D1: Sets the destination register for storing received data. For example, if D1 = D10, the incoming data will be saved starting at D10.
- D2: Configures the reception completion flag. When data transmission finishes, the flag turns ON, signaling the process is complete.
ETHRS Config in Action
Below is the logic for Modbus TCP transmission of data registers through ETHRS API.
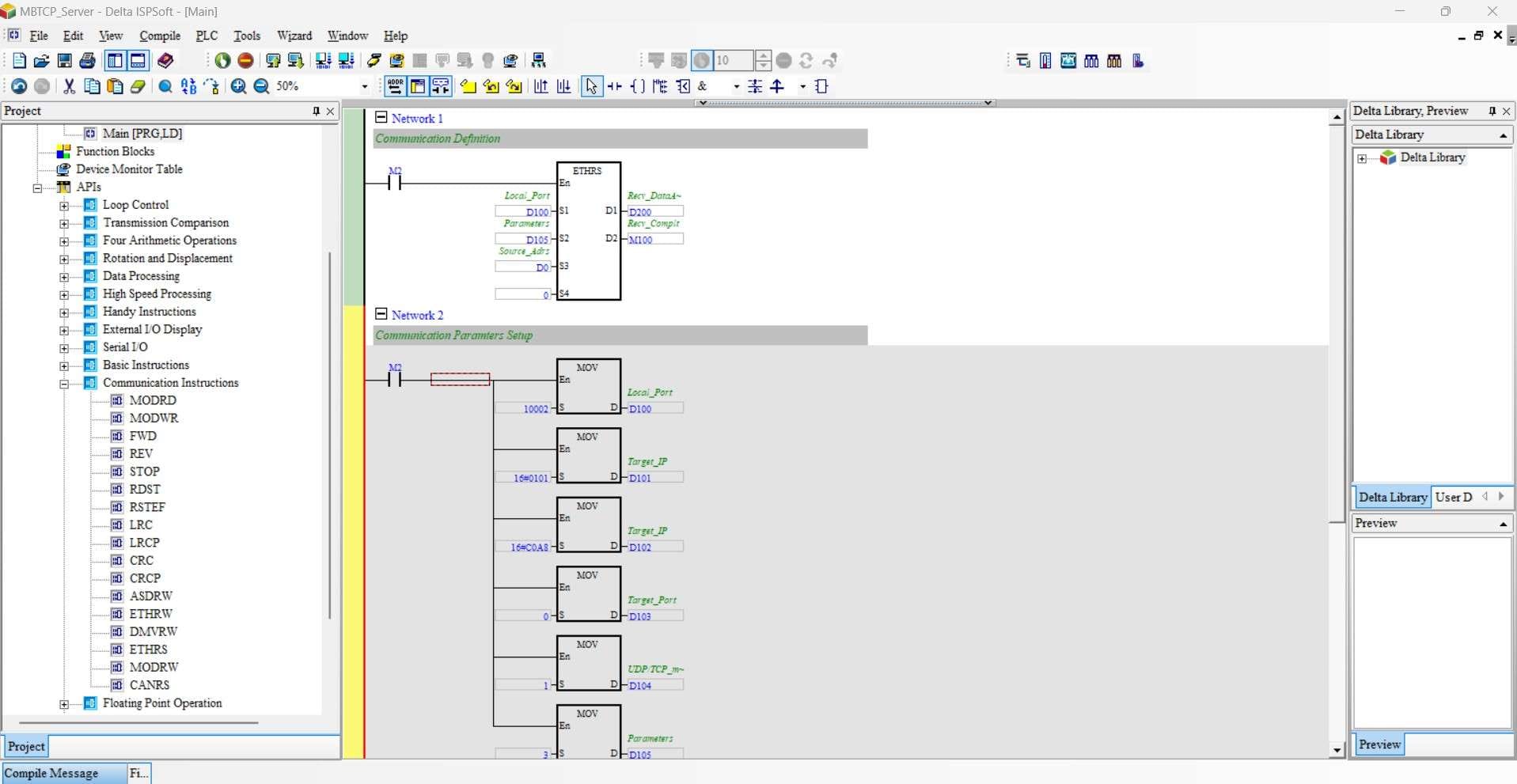
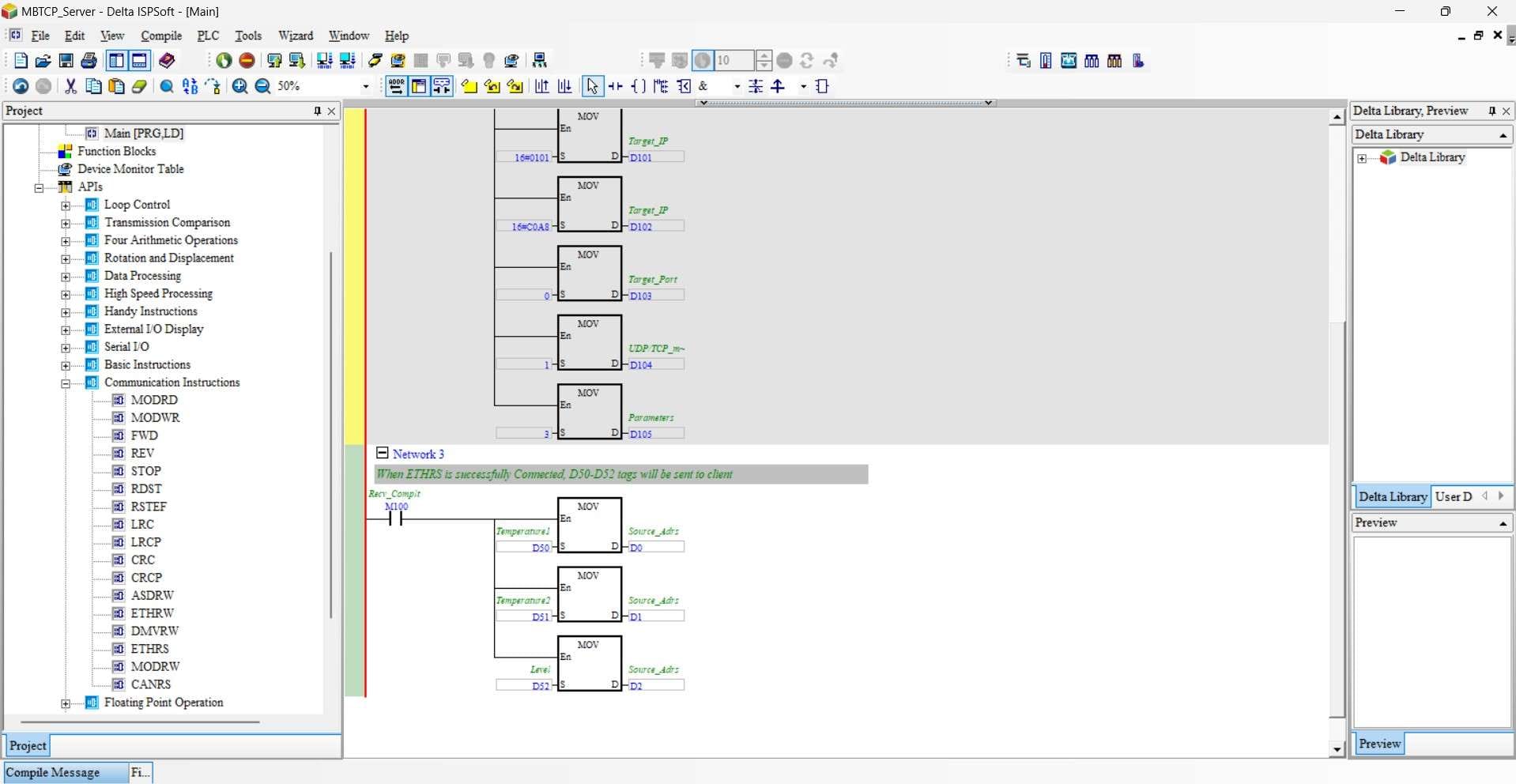
Step 4: Select the Driver and Download the PLC Program
After creating logic for Modbus TCP communication, head towards the "tools" tab. Select Communication Settings. A new window will pop up. Select Driver from the drop-down in the Driver option that we created in the COMMGR application and then click on "OK."
Now, the final step is to compile the project to make sure there are no errors in it and then download it to the PLC memory. If successful, the PLC will act as a Modbus TCP server, ready for communication.
Verify Modbus Data using the ModbusClientX Tool
To verify that your PLC is functioning correctly as a Modbus TCP server, use the ModbusClientX tool to poll the PLC for Modbus data.
- Open ModbusClientX and select Modbus TCP.
- Enter your Delta PLC’s IP address and click on “connect.”
- Click on “read from 0 to 9” to retrieve the first 10 data values stored from D0 to D10 within the PLC. Here, we are just moving 3 registers from the logic to the ModbusClientX.
D0 = 40001
D1 = 40002 and so on.
Next, return to ISPSoft and turn on the “Monitor Mode”. The values that appear in the ModbusClientX are successfully sent from the PLC. It confirms successful data reading from the PLC to the ModbusClientX.
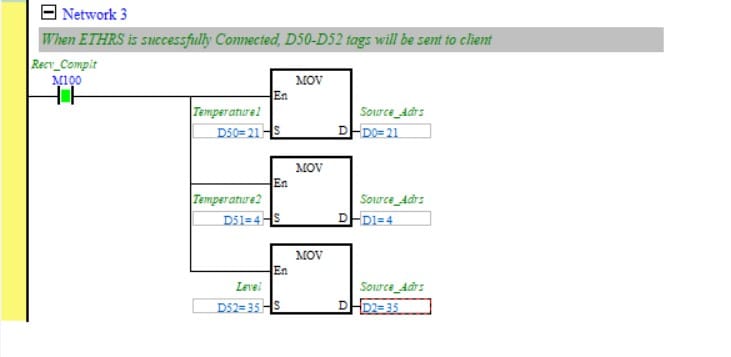
Next Steps: Send PLC Data to the Cloud
Modern industrial automation relies on the seamless integration of devices, and IoT gateways are key to integrate PLC data with cloud applications—such as Ubidots. Acting as a bridge between your Delta PLC and the cloud, these devices ensure secure, efficient, and scalable data transfer. Whether you're tracking production metrics or enabling predictive maintenance, an IoT gateway is the key to unlocking actionable insights from your PLC data.
What is an IoT Gateway?
An IoT gateway serves as a communication hub between your Delta PLC and external systems, including industrial IoT platforms. It translates data from protocols like Modbus TCP, Modbus RTU, BACnet or OPC-UA to cloud-friendly protocols such as HTTP or MQTT, ensuring a seamless flow of information to the Internet. By preprocessing and aggregating data from multiple machines and sensors, IoT gateways are the door to smarter automation.
Choosing the Right IoT Gateway
Selecting a Modbus-compatible IoT gateway is crucial for successful integration. To simplify the process, we’ve compiled a list of the top Modbus-compatible IoT gateways to help you find the perfect match for your application.
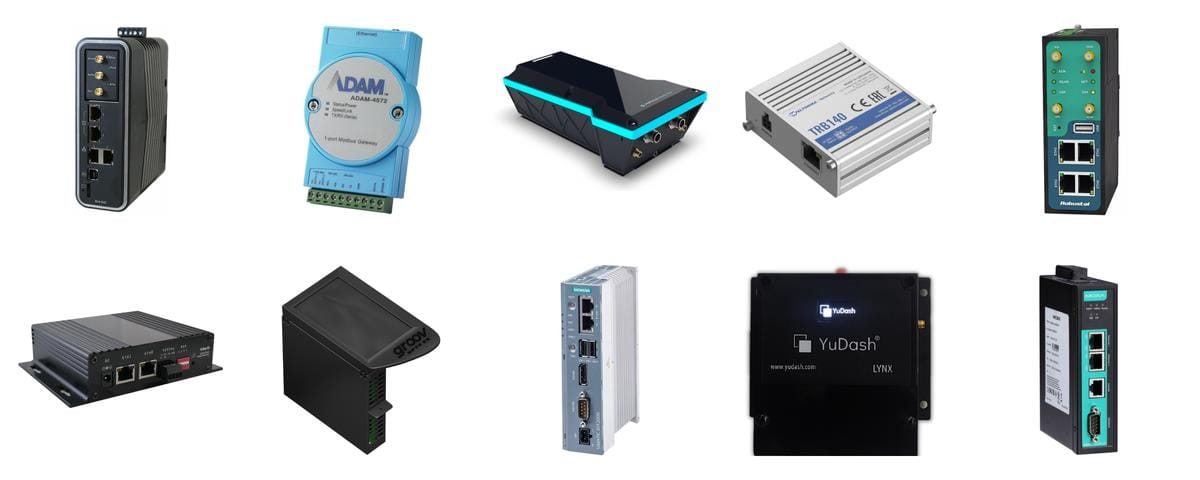
Some IoT gateways like the Advantech's ADAM 6717, PUSR USR-M300 and Elastel EG324 come with Node-RED pre-installed, a powerful flow-based programming tool for IoT and industrial automation. Node-RED includes a widely used library called node-red-contrib-modbus, which allows you to poll data from your Delta PLC over Modbus TCP seamlessly. This makes it easier to configure, maintain, and customize data flows to meet your specific needs.
Send Delta PLC Data to the Ubidots Cloud
Connecting your Delta PLC to the Ubidots cloud is a game-changer for industrial monitoring and control. By leveraging IoT tools like Node-RED and MQTT, you can seamlessly push real-time PLC data to Ubidots, where it can be transformed into intuitive dashboards, alerts, and analytics.
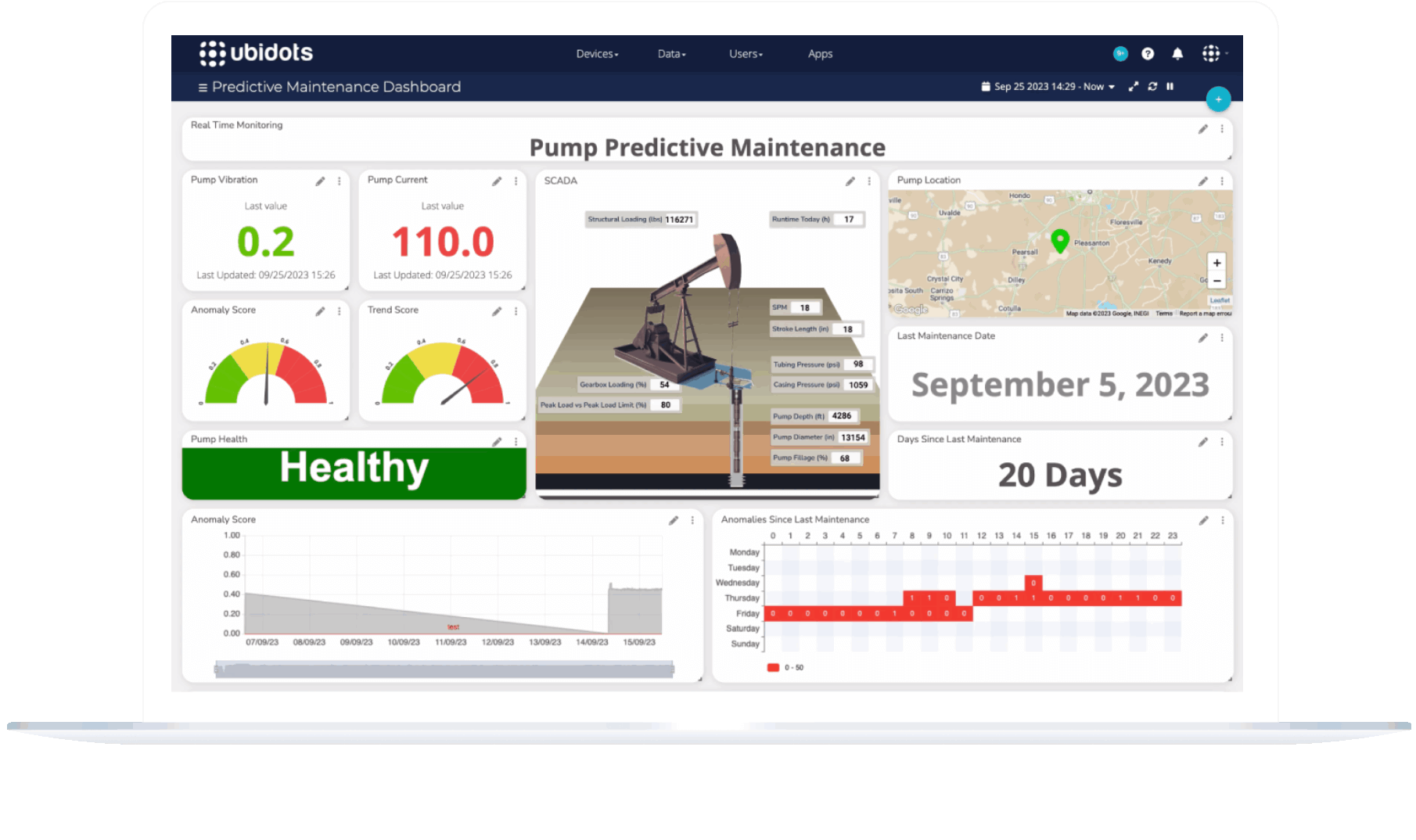
To make this process easier, we’ve prepared a comprehensive guide to sending PLC data to the cloud using Node-RED and MQTT. This guide walks you through the steps required to read Modbus TCP registers using Node-RED and start visualizing data in Ubidots.
With Ubidots, the possibilities are endless. Monitor key metrics, set up intelligent alarms, or even integrate predictive maintenance solutions—all from a single platform. By combining the power of your Delta PLC with Ubidots’ versatile cloud capabilities, you unlock the potential to streamline operations and make data-driven decisions with ease.
Frequently Asked Questions (FAQs)
What is Modbus TCP?
Modbus TCP is an Ethernet-based variant of the Modbus communication protocol, designed to facilitate real-time data exchange in industrial automation. It simplifies the connection of devices like PLCs, sensors, and actuators by leveraging standard TCP/IP networking, allowing seamless communication across modern industrial environments. Unlike Modbus RTU, which operates over serial communication, Modbus TCP is ideal for high-speed, scalable networks where reliability and accessibility are crucial.
What is an IoT Gateway?
An IoT gateway is a device that connects industrial equipment, like Delta PLCs, to the cloud, enabling seamless data exchange and advanced analytics. It acts as a translator, converting data from industrial protocols such as Modbus TCP or RTU into internet-friendly formats like MQTT or HTTP. Beyond translation, IoT gateways often preprocess and aggregate data, enhancing efficiency and reducing network strain. These gateways are vital for real-time monitoring, predictive maintenance, and integrating factory operations into smart IoT ecosystems.
What are the benefits of sending data in real time to the cloud?
Sending data in real time to the cloud unlocks powerful advantages for industrial automation. It enables instant monitoring and control of processes from anywhere, reducing downtime and improving decision-making. With real-time data, predictive maintenance becomes possible, helping to prevent costly equipment failures. Cloud integration also allows for advanced analytics, turning raw data into actionable insights that drive efficiency and optimize performance. Ultimately, it enhances scalability, collaboration, and the overall agility of operations in a connected industrial ecosystem.
What is Delta in PLC?
Delta refers to a renowned manufacturer of programmable logic controllers (PLCs) and automation solutions, known for their reliability, versatility, and cost-effectiveness. Delta PLCs, such as the DVP series, are widely used in industrial automation for tasks ranging from simple control processes to complex system integrations. They support various communication protocols, including Modbus TCP, making them ideal for connecting with IoT platforms and ensuring seamless data exchange across modern industrial networks. Delta’s focus on performance and affordability has made their PLCs a popular choice for businesses seeking scalable and efficient automation solutions.
What software is used to program Delta PLC?
Delta PLCs are programmed using ISPSoft and WPLSoft, with the choice depending on the PLC model and complexity of the project. ISPSoft is the advanced option, supporting modern PLCs like the DVP-SE series and offering multiple programming languages, including Ladder Diagram (LD), Function Block Diagram (FBD), and Structured Text (ST). It also enables features like Modbus TCP configuration for Ethernet-based communication. WPLSoft, on the other hand, is designed for older Delta PLC models and provides a straightforward interface with Ladder Logic programming. Both tools ensure efficient and flexible programming for a wide range of automation needs.
What is the Delta PLC Protocol?
Delta PLCs support multiple communication protocols to ensure seamless integration with industrial systems. Among the most common is Modbus, available in both RTU (serial communication) and TCP (Ethernet-based) variants. These protocols allow Delta PLCs to interact with a wide range of devices, including sensors, actuators, and IoT gateways. Modbus TCP, in particular, is widely used for high-speed data exchange in modern industrial environments, enabling real-time monitoring, control, and connectivity with cloud platforms. This versatility makes Delta PLCs a reliable choice for diverse automation needs.
What is ISPSoft?
ISPSoft is Delta Electronics' advanced programming software for their programmable logic controllers (PLCs), adhering to the IEC 61131-3 standard. It integrates multiple tasks for project management and supports five programming languages: Ladder Diagram (LD), Function Block Diagram (FBD), Sequential Function Chart (SFC), Instruction List (IL), and Structured Text (ST). ISPSoft facilitates hardware and network configuration, motion programming, and offers features like data tracing and logging, providing a comprehensive environment for developing both simple and complex control systems.
What is the difference between WPLSoft and ISPSoft?
WPLSoft and ISPSoft are both programming tools for Delta's PLCs, each tailored to different needs. WPLSoft is designed for simpler applications, offering an intuitive interface focused on Ladder Diagram programming, making it ideal for straightforward control tasks. In contrast, ISPSoft is a more advanced platform that supports multiple programming languages, including Ladder Diagram (LD), Function Block Diagram (FBD), and Structured Text (ST), aligning with the IEC 61131-3 standard. It integrates hardware and network configuration, motion control programming, and provides features like task assignment, function blocks, and variable declarations, catering to complex and large-scale automation projects.
Is Delta PLC software free?
Yes, Delta Electronics offers free programming software for their PLCs. For instance, WPLSoft is available at no cost and is suitable for programming Delta's DVP series PLCs. Additionally, ISPSoft, which supports multiple programming languages and advanced features, can be downloaded without charge from Delta's official website. These tools provide comprehensive solutions for developing and managing automation projects with Delta PLCs.
Do PLCs use Modbus?
Yes, many PLCs, including Delta models, use Modbus as a communication protocol. Modbus enables seamless data exchange between devices like sensors, actuators, and PLCs, making it a popular choice in industrial automation. It supports both serial communication (Modbus RTU) and Ethernet-based networks (Modbus TCP), providing flexibility for various applications. This protocol is widely recognized for its simplicity, reliability, and ability to integrate devices from different manufacturers, ensuring smooth and efficient system operation.