A Quick Tutorial on Rockwell PLC: ControlLogix as Modbus TCP Server
This guide demonstrates how to configure the ControlLogix 5580 L85E PLC as a Modbus TCP server, using the Modbus TCP Server Add-On Instruction (AOI). Follow along to meet your automation needs efficiently while maintaining the highest standards of operation and reliability.
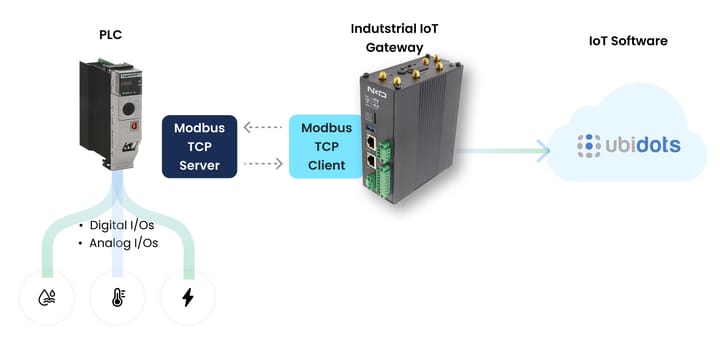
In the world of industrial automation, Allen-Bradley programmable logic controllers (PLCs) by Rockwell Automation stand as a benchmark for reliability and advanced performance. The ControlLogix series is designed for large-scale, complex systems that demand precision and scalability. Integrating these PLCs with Modbus devices enhances their connectivity, allowing seamless communication with third-party equipment—and even empowering operations to send valuable data from the PLC to industrial IoT platforms in the cloud, enabling better remote monitoring and proactive maintenance.
This guide demonstrates how to configure the ControlLogix 5580 L85E PLC as a Modbus TCP server, using the Modbus TCP Server Add-On Instruction (AOI). Follow along to meet your automation needs efficiently while maintaining the highest standards of operation and reliability.
Introduction to Modbus and Rockwell Automation/Allen-Bradley PLCs
What is Modbus?
Modbus is a widely used communication protocol developed in 1979 by Modicon, now part of Schneider Electric. It enables seamless communication between devices in industrial automation systems, serving as a bridge for sharing data across networks. Designed for simplicity and versatility, Modbus is foundational in many automation setups.
At its core, Modbus operates as a master-slave protocol (or client-server in Modbus TCP), where a single device, known as the master, initiates communication by requesting data from one or more slave devices. This setup is ideal for real-time monitoring and control of equipment like sensors, actuators, and PLCs.
The protocol supports multiple communication modes, making it adaptable to a variety of environments:
- Modbus RTU: A protocol optimized for serial communication over RS-485 or RS-232 networks.
- Modbus TCP: Built to leverage Ethernet networks, providing faster, more reliable communication for modern industrial systems.
Its simplicity and open design have made Modbus a popular choice for interoperability between devices from different manufacturers. This ease of integration ensures smooth operation in complex systems, whether you're transmitting basic data or orchestrating intricate automation processes.
By using Modbus, industrial operations access a robust and flexible communication standard, perfect for connecting a diverse range of devices.
Understanding Modbus TCP Protocol
Modbus TCP is a widely used protocol for communication between devices over IP networks. Originally developed for serial communication, Modbus has evolved to meet the demands of modern industrial automation by leveraging Ethernet networks. This evolution has resulted in Modbus TCP, which offers faster and more reliable communication between devices.
In industrial automation, Modbus TCP is essential for enabling seamless data exchange between various components, including programmable logic controllers (PLCs), control systems, and other automation equipment. By utilizing Ethernet, Modbus TCP ensures that data is transmitted quickly and efficiently, which is crucial for real-time monitoring and control.
Why Choose an Allen-Bradley ControlLogix PLC?
Allen-Bradley ControlLogix PLCs are renowned for their performance, reliability, and flexibility in industrial automation. As part of a brand with a legacy dating back to 1903, Allen-Bradley products have become a cornerstone for businesses requiring advanced, scalable control solutions.
The ControlLogix series stands out as a top-tier choice for complex, large-scale systems, offering unmatched processing power and seamless integration capabilities. These PLCs are engineered to handle demanding tasks, making them a favorite in industries where precision and speed are critical.
Allen-Bradley PLCs are programmed with Studio 5000, a user-friendly software suite that simplifies programming and enhances development efficiency. From ladder logic to structured text, the software provides the tools necessary to build complex automation processes with ease.
Here’s why the ControlLogix control system remain a trusted choice:
- Processing Power: Designed to execute large-scale, data-intensive applications without delays.
- Reliability: From conformal coating to protect the board, to the use of industrial-grade materials, ControlLogix PLCs are built to withstand harsh industrial environments, ensuring consistent operation and reduced downtime.
- Flexibility: Supports multiple communication protocols and programming languages, enabling seamless integration with diverse systems.
- Safety Features: Includes fail-safe options for critical operations, ensuring that systems can operate securely under all conditions.
For organizations that prioritize quality, innovation, and performance, the ControlLogix PLC provides a comprehensive automation solution. Using these products eliminates manual work to a high degree, bringing levels of efficiency into companies that are instrumental to remain competitive in any industrial context. While Allen-Bradley products may come at a higher price compared to other brands, their ability to deliver long-term value and reduced total cost of ownership makes them an indispensable investment for businesses aiming to stay ahead in today’s competitive landscape.
Types of Allen-Bradley Programmable Logic Controllers
Allen-Bradley PLCs, manufactured by Rockwell Automation, are designed to cater to a wide range of industrial automation needs. From compact controllers for small systems to high-performance solutions for complex operations, the variety of PLCs ensures there’s a model suitable for every application.
MicroLogix
Compact, cost-effective, and perfect for small-scale automation tasks, the MicroLogix series is ideal for businesses looking for affordable yet reliable solutions. Despite its compact size, it offers robust programming capabilities and is suitable for simple industrial automation tasks.
CompactLogix
Positioned as a mid-range option, CompactLogix PLCs provide a balance of scalability and performance. They are designed for medium-complexity applications and can handle more significant automation tasks compared to MicroLogix. With support for EtherNet/IP and add-on instructions, CompactLogix is a versatile choice for growing businesses.
ControlLogix
The flagship series for large-scale, complex systems, ControlLogix PLCs offer unparalleled processing power, flexibility, and modularity. These controllers are built for demanding applications that require seamless integration, real-time communication, and advanced safety features. With support for Modbus TCP, ControlLogix PLCs are at the forefront of modern industrial automation technologies. The ControlLogix series represents a significant improvement over previous models, offering enhanced processing power and advanced safety features.
PLC-5
A legacy series, PLC-5 controllers were known for their reliability and robust design, making them a staple in automation for decades. While they are no longer the go-to choice for new projects, many facilities still rely on them for critical operations, especially in applications requiring Data Highway Plus communication.
SLC 500
Another legacy series, the SLC 500 controllers served as mid-range options before the introduction of CompactLogix. While now mostly replaced, these PLCs were renowned for their durability and ease of use, making them a valuable tool for automation professionals during their peak.
Model | Best For | Connectivity | Scalability | Comments |
MicroLogix | Small-scale automation tasks | Basic Ethernet, RS-232 | Low | Compact and cost-effective for simple tasks. |
CompactLogix | Medium-complexity systems | EtherNet/IP, Modbus TCP | Moderate | Ideal for growing operations needing flexibility. |
ControlLogix | Large-scale, complex systems | EtherNet/IP, Modbus TCP | High | Industry-leading performance and modularity. |
PLC-5 | Legacy systems | Data Highway Plus | Limited | Still in use but phased out for newer systems. |
SLC 500 | Legacy mid-range systems | Ethernet, RS-485 | Limited | Durable, but mostly replaced by modern models. |
MVI56-MCM Module as Modbus Bridge for Allen-Bradley PLCs
In this article, we will explore how Rockwell’s AOIs simplify automation tasks, particularly in enabling Modbus communication. However, AOIs are not the only way to achieve Modbus functionality. Automation engineers often rely on third-party modules like the MVI56-MCM to bridge the gap between Allen-Bradley PLCs and Modbus-compatible devices.
An AOI is like reusable code in software development. Imagine you’re writing a software application and have a block of code that performs a specific task. Instead of rewriting this block every time you need it, you encapsulate it in a function or module that you can call wherever it’s needed. An AOI is essentially the PLC equivalent of this reusable function.
In the past, Rockwell Allen-Bradley PLCs did not include a native AOI for Modbus TCP communication. Automation engineers often had to rely on third-party expansion modules, such as the MVI56-MCM by ProSoft Technology, to enable Modbus protocol support for ControlLogix PLCs. These modules served as dedicated protocol translators and handled the Modbus communication externally, bridging the gap between the Allen-Bradley PLC and Modbus-compatible devices.
The communication between the PLC and the MVI56-MCM module occurred through the ControlLogix backplane, a shared communication bus that connects all modules within the PLC rack. The module was configured in the ControlLogix PLC program (using RSLogix 5000 or Studio 5000) as a generic I/O module, and data exchange was achieved using Input/Output (I/O) memory mapping.
On the Modbus side, the MVI56-MCM acted as either a Modbus RTU Master/Slave or a Modbus TCP Client/Server, depending on the application and configuration. It managed Modbus communication independently, handling tasks like polling Modbus devices, managing requests, and formatting data into Modbus-compliant frames.
On the PLC side, the MVI56-MCM presented Modbus data as predefined memory blocks accessible via the PLC program. Engineers could read and write to these memory blocks using PLC logic.
Requirements
Hardware Requirements
- ControlLogix L85E PLC
- EN2T or EN2TR EtherNet/IP module
- 10-slot chassis for PLC and EtherNet/IP module
- Ethernet cable
Software Requirements
- Studio 5000 (formerly RsLogix 5000) version 20 or higher
- Modbus TCP AOI v2.04
- RSLinx
- Modbus ClientX
Step-by-Step Guide
Step 1: Install Studio 5000
Download and install Studio 5000 from the Rockwell Product Compatibility and Download Center. Ensure you have version 20 or higher to support the required programming capabilities.
Step 2: Configure the Studio 5000 Project
-
Open Studio 5000 and click on ‘New Project’. In the new window, select ‘Logix’ in the left pane and then select ‘ControlLogix 5580 Controller’ ⟶ ‘1756-L85E ControlLogix 5580 Controller’.
-
In the new window, select ‘Logix’ in the left pane and then select ‘ControlLogix 5580 Controller’ ⟶ ‘1756-L85E ControlLogix 5580 Controller’.
-
Set the revision field according to your version of Studio. Since we are using the 32, we use this number. Configure the chassis and slot based on your hardware setup and click on ‘Finish’.
-
Add an EtherNet/IP module (EN2T in our case):
Right-click the backplane in the IO configuration tree and click on ‘New Module’.
Look for the EN2T module and click on ‘Create’.
Enter the module’s IP address, slot number, and name.
Step 3: Download AOI and Configure the Task
- Head to this Rockwell link and download the file called ‘Modbus TCP Add-On instructions for ControlLogix and CompactLogix controllers, AOI Version 2.04.00’.
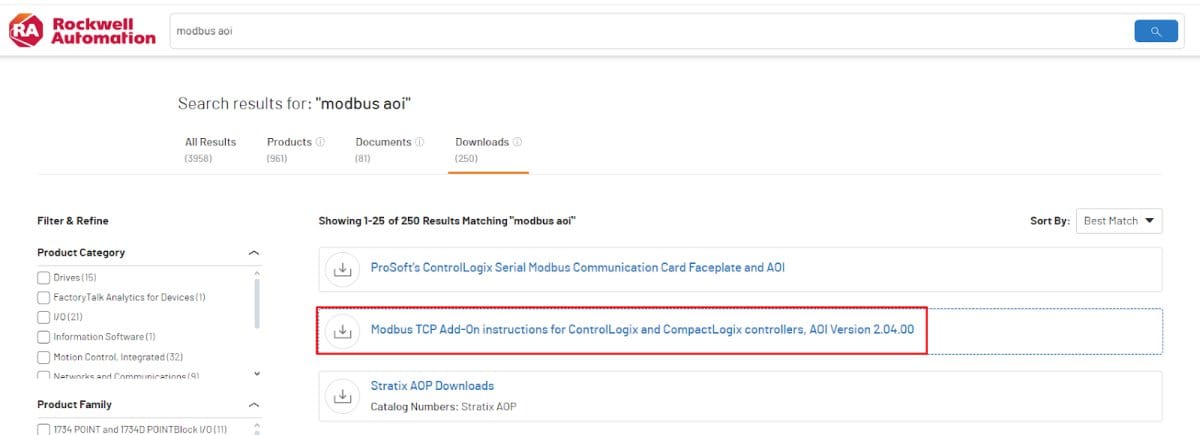
- Back in Studio 5000, right click on ‘Tasks’ ⟶ ‘New Task’. Name the task, ensure its ‘type’ is periodic, and define the period. Rockwell recommends the rate to be 10ms or higher (slower rates will reduce controller load and reduce performance, while faster rates will increase performance but will add a significant load to the controller).
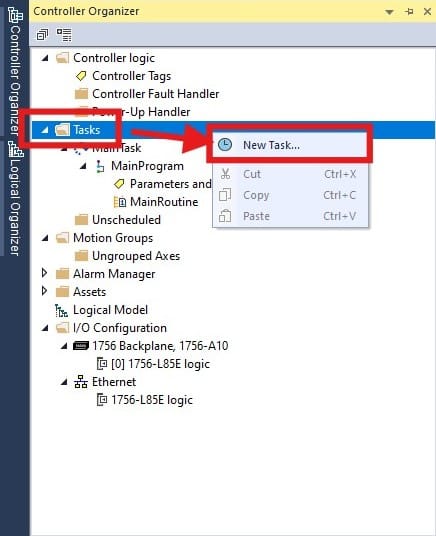
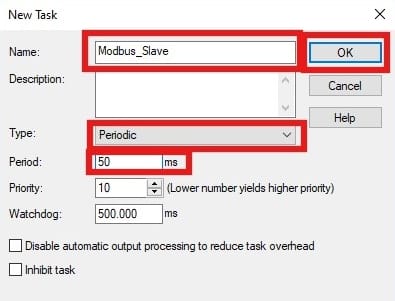
- Create a program within the new task. Do it by right clicking in the task ⟶ ‘Add’ ⟶ ‘New Program’. Name it.
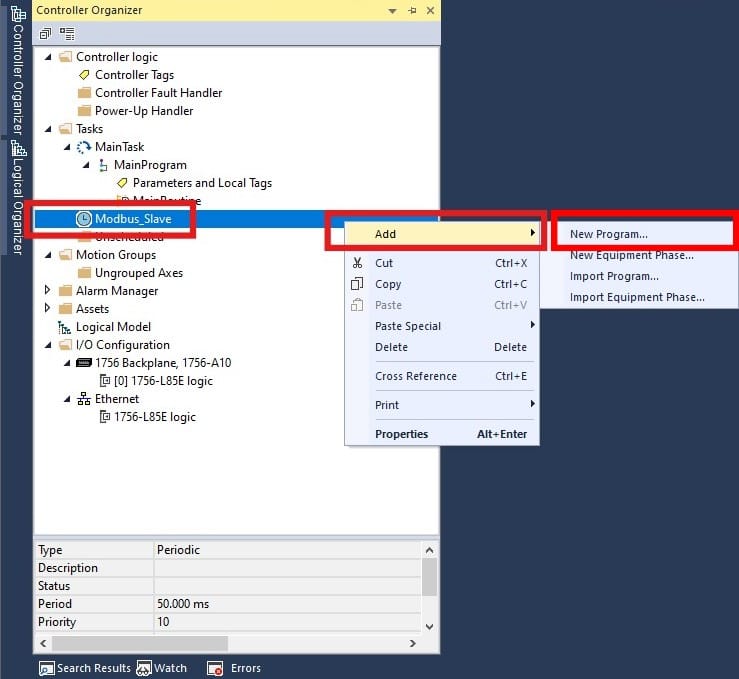
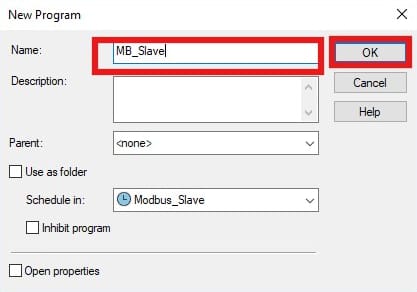
- Now we will create a new routine within this new program. Do this by right clicking on the program ⟶ ‘Add’ ⟶ ‘New Routine’. Name it.
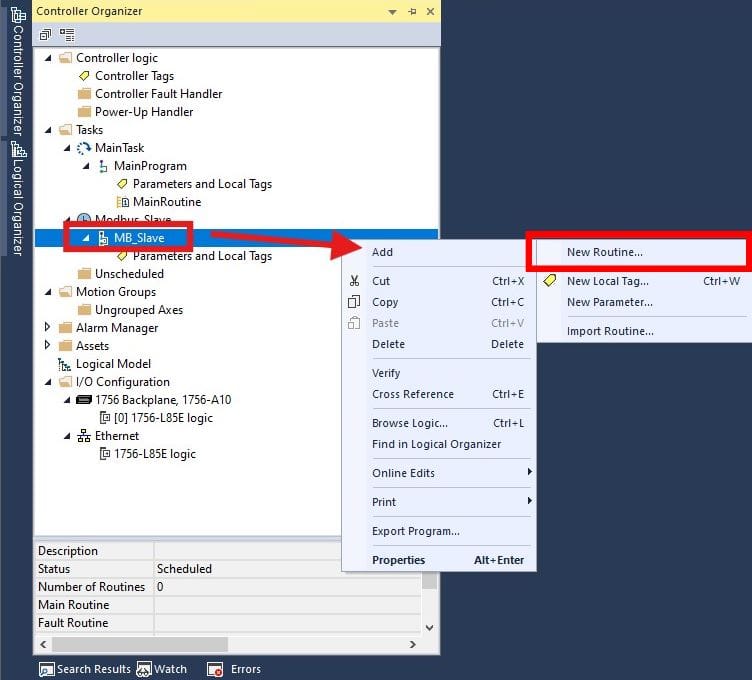
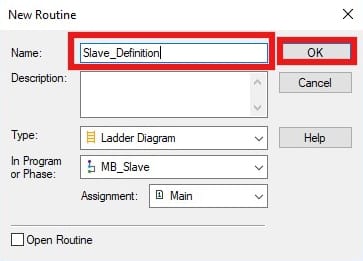
- Open the routine, right click on the left side of the routine and click on ‘Import Rungs’. A pop-up will appear, look for the folder where you downloaded the AOI (within the ‘Logic’ file), select the ‘raC_Opr_NetModbusTCPServer_Rung.L5X’ file. The Modbus TCP AOI will be added into the routine.
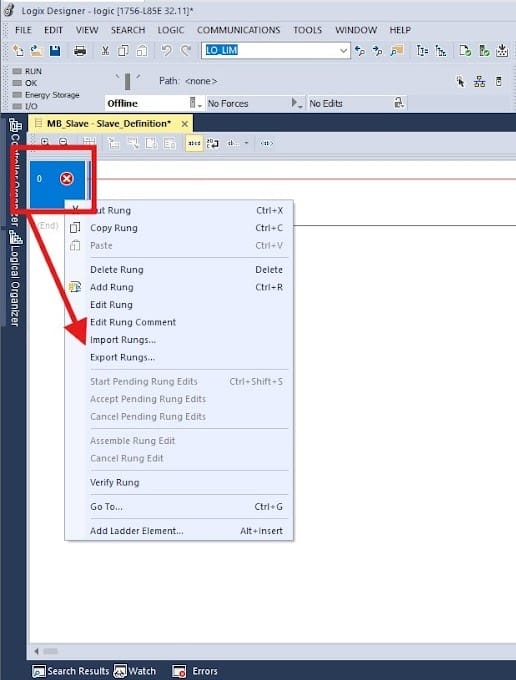
- After adding the routine, right-click on the AOI tag and press ‘Monitor Server_01’. Here, define the EtherNet/IP module’s slot and IP address. In our case, ‘1’ is the slot and ‘192.168.1.13’ is the IP address of the module. The remaining parameters are left as they are.
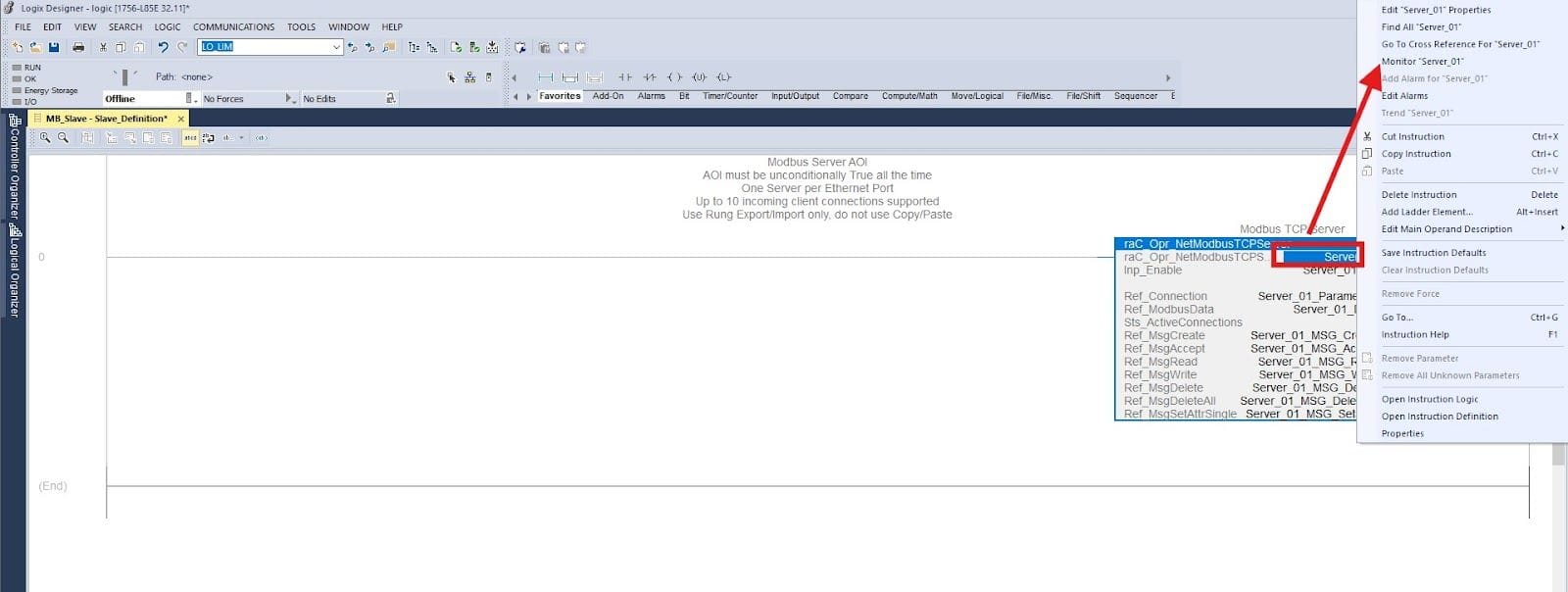
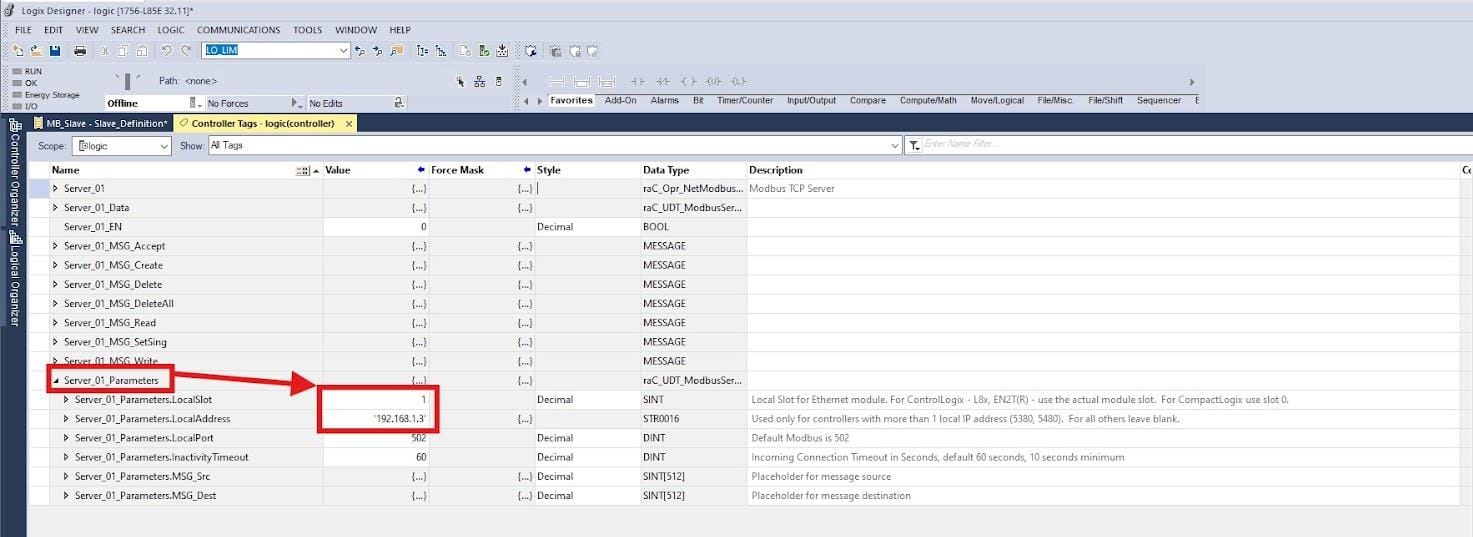
- Now the final step is to verify there are no errors in the project and then download it to the PLC. If successful, the PLC will act as a Modbus TCP server. Head towards the ‘Communication’ tab. Select ‘Who Active’.
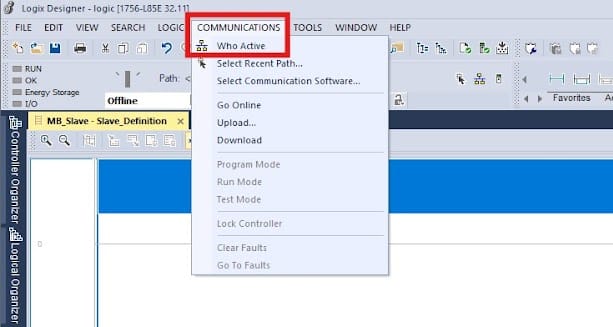
- A new window will pop up for RSLinx. Select your controller and press ‘Download’. The controller will go in ‘Online’ or you can change it as shown in the picture.
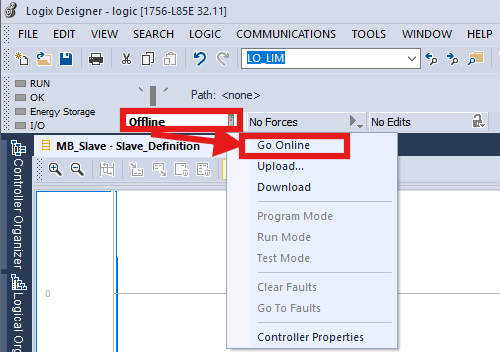
Step 4: Test Modbus Communication With ModbusClientX
To verify that your PLC is working correctly as a Modbus TCP server, use the ModbusClientX tool to poll the PLC for Modbus data.
- Open ModbusClientX and select Modbus TCP.
- Enter the PLC’s IP address and click on ‘Connect’.
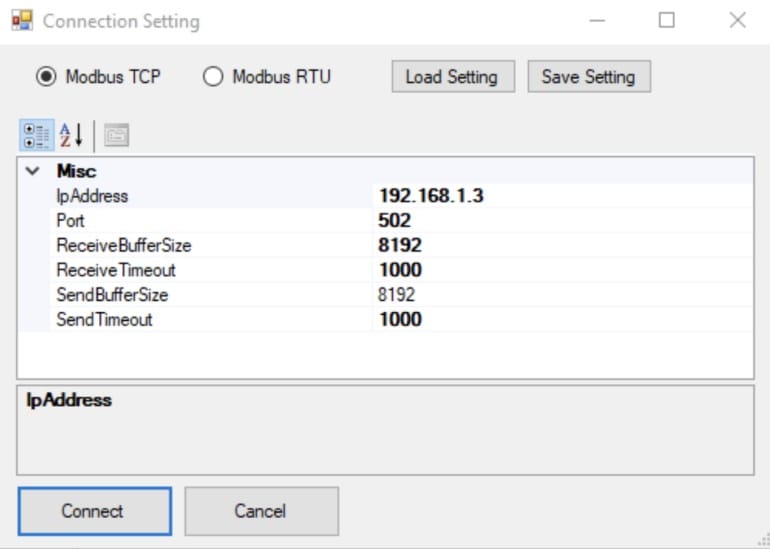
- Click on “Read from 0 to 9” to retrieve the first 10 data values stored from Server_01_Data.HoldRegisters_4xxx[0] to Server_01_Data.HoldRegisters_4xxx[9]. Here, we are just moving 3 registers from the logic to the ModbusClientX.
Server_01_Data.HoldRegisters_4xxx[0] = 40000
Server_01_Data.HoldRegisters_4xxx[1] = 40001
…
Server_01_Data.HoldRegisters_4xxx[9] = 40009
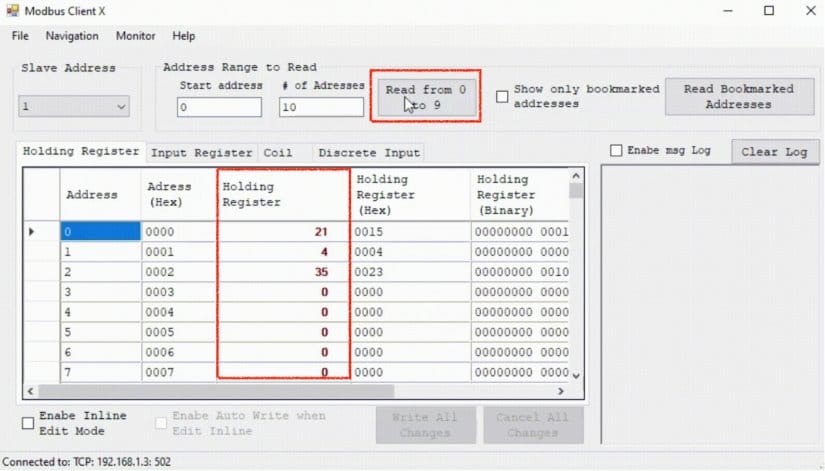
- Return to Studio 5000. If the values sent from the PLC appear in ModbusClientX, this confirms a successful data reading.
FAQs
Do PLCs use Modbus?
Yes, PLCs commonly use Modbus for communication in industrial automation. Modbus enables seamless data exchange between devices, such as sensors, actuators, and control systems, ensuring interoperability even among devices from different manufacturers. Many PLCs, including the Allen-Bradley ControlLogix series, support Modbus TCP, which leverages Ethernet for fast and reliable communication, making it a preferred choice for modern, networked industrial systems.
Is Rockwell the same as Allen-Bradley?
Rockwell is the parent company of Allen-Bradley, a renowned brand under its umbrella. Allen-Bradley specializes in manufacturing programmable logic controllers (PLCs), industrial control systems, and automation products. While Allen-Bradley focuses on the hardware and solutions, Rockwell oversees the broader portfolio, including software, services, and advanced automation technologies, making the two closely intertwined but not identical.
What is ControlLogix used for?
ControlLogix is a line of high-performance programmable logic controller (PLC) from Allen-Bradley, designed for managing complex, large-scale industrial automation systems. It is used to control and monitor processes, machinery, and production lines with precision and scalability. ControlLogix PLCs are ideal for applications requiring seamless integration, real-time communication, and advanced safety features, making them a preferred choice in industries like manufacturing, energy, and logistics. Their modular design and support for multiple communication protocols, including Modbus TCP, enhance flexibility and efficiency in demanding automation environments.
What are Allen-Bradley PLCs?
Allen-Bradley PLCs are advanced programmable logic controllers developed by Rockwell, designed to automate and optimize industrial processes. Known for their reliability and flexibility, these PLCs range from compact controllers like the MicroLogix series for small-scale tasks to high-performance solutions like the ControlLogix series for large, complex systems. Allen-Bradley PLCs support a variety of communication protocols, including EtherNet/IP and Modbus TCP, ensuring seamless integration with diverse industrial equipment and networks. With robust performance and extensive programming capabilities, they are a cornerstone in modern automation.
What is the difference between Rockwell Automation and Allen-Bradley?
Rockwell Automation is the parent company, a global leader in industrial automation and digital transformation solutions. Allen-Bradley is a flagship brand under Rockwell, specializing in hardware products like programmable logic controllers (PLCs), motor control systems, and industrial components. While Rockwell encompasses a broad portfolio, including software and services, Allen-Bradley focuses on delivering high-quality hardware for automation systems. Together, they provide comprehensive solutions for industrial operations worldwide.
What is ControlLogix 5580?
The ControlLogix 5580 is a high-performance programmable logic controller (PLC) from Allen-Bradley, part of the ControlLogix series. It is designed for complex industrial automation tasks that require advanced processing power, real-time communication, and enhanced safety features. With built-in Ethernet capabilities and support for protocols like Modbus TCP and EtherNet/IP, the 5580 provides faster data handling and improved system scalability. Its modular design allows seamless integration with various industrial applications, making it a preferred choice for demanding automation environments.
What is Studio 5000 software used for?
Studio 5000 is the integrated development environment (IDE) for programming and configuring Allen-Bradley programmable logic controllers (PLCs), including the ControlLogix and CompactLogix series. It streamlines the development of industrial automation systems by supporting multiple programming languages, such as Ladder Diagram (LD) and Structured Text (ST). Studio 5000 is used for designing, simulating, and managing control applications, enabling seamless configuration of hardware, communication, and advanced safety features. Its intuitive interface enhances efficiency, making it a cornerstone tool for modern industrial automation projects.
Does ControlLogix support Modbus TCP?
Yes, ControlLogix PLCs support Modbus TCP through the use ofAOIs or dedicated modules like the MVI56-MCM. This allows them to talk to Modbus-compatible devices over Ethernet networks. By enabling Modbus TCP, ControlLogix PLCs can exchange real-time data with third-party equipment, making them highly adaptable for diverse industrial automation systems.
What protocol does Allen-Bradley PLC use?
Allen-Bradley PLCs support a variety of communication protocols to ensure flexibility and seamless integration in industrial environments. These include EtherNet/IP for high-speed Ethernet communication, DeviceNet for device-level networking, ControlNet for real-time control, Remote I/O for distributed input/output systems, and RS-232 / RS-485 serial protocols. This diverse protocol support makes Allen-Bradley PLCs adaptable to a wide range of automation needs.
What is the Modbus TCP protocol?
Modbus TCP is an Ethernet-based communication protocol used in industrial automation to exchange data between devices like PLCs, sensors, and control systems. It extends the traditional Modbus protocol by leveraging TCP/IP for faster, more reliable communication over Ethernet networks. Modbus TCP operates on a client-server model, enabling seamless real-time data sharing across diverse equipment. Its simplicity, scalability, and compatibility with devices from multiple manufacturers make it a standard choice for modern industrial systems.