10 Benefits of Predictive Maintenance in IoT Projects
IoT predictive maintenance is an asset management technique that identifies machine failure before it happens. Find here 10 benefits in IoT projects.
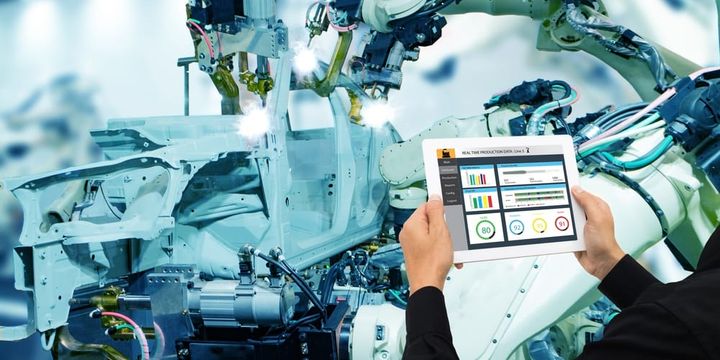
The Internet of things (IoT) has opened a wide range of possibilities. One of the most revolutionary applications of the IoT is predictive maintenance in manufacturing plants.
» FREE TRIAL: Launch Your IoT Application To Market in Less Than 30 Days with Ubidots IoT Device Management Dashboard
IoT-based predictive maintenance enables more efficient use of existing assets by providing the ability to predict machine failures and reduce maintenance issues.
It can help identify the causes of delays, whether internal or external, and in setting up processes to address these causes.
What Is IoT Predictive Maintenance
IoT predictive maintenance entails maintaining a system by identifying a fault before it happens.
Therefore, IoT predictive maintenance is the use of IoT technology to study a production system in real time and forecast when and how a malfunction might occur in its components.
IoT maintenance systems collect real-time data of a machine’s operating conditions and use software to analyze that data to create performance reports.
During this process, any potential glitches and breakdowns can be spotted and mitigated proactively. On the other hand, reactive maintenance involves fixing a component only after it has broken down.
The IoT makes predictive maintenance much more accurate and efficient. In turn, it provides a range of benefits for manufacturers.
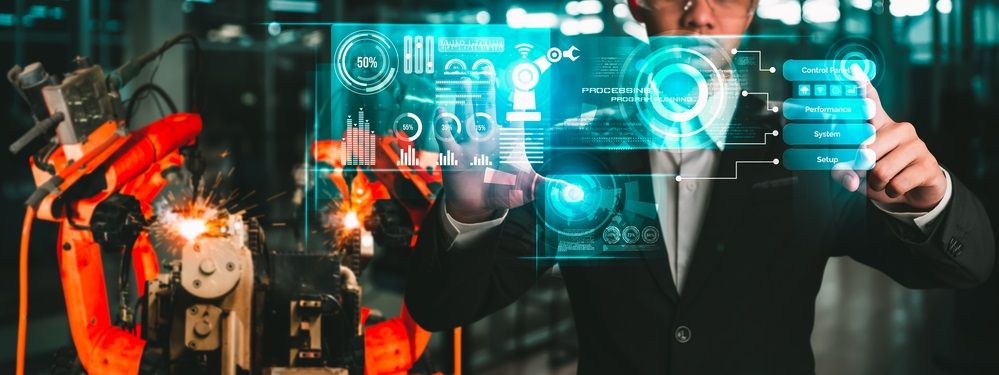
Benefits of IoT Predictive Maintenance
Lower Maintenance Costs
Machines will always require maintenance as a result of exertion and unforeseen mechanical failure.
With an IoT predictive maintenance system, you can anticipate a breakdown before it happens, giving you the leverage to plan for damage before it worsens.
Management consulting firm McKinsey reports that predictive maintenance reduces costs related to factory equipment by 40%.
Enhanced Production
When equipment breaks down unexpectedly, the production capacity of a manufacturing plant reduces during the downtime.
IoT predictive maintenance resolves such events by forecasting machine failure and proposing solutions in due time. Consequently, production follows the planned schedule.
Improved Utilization of Machines
Since IoT predictive maintenance identifies issues before they arise, machines last longer. Unlike preventive maintenance, which fixes damages after they happen, predictive maintenance spots which components need to be replaced before they break down completely.
This method of monitoring equipment therefore extends the useful lifetime of your assets.
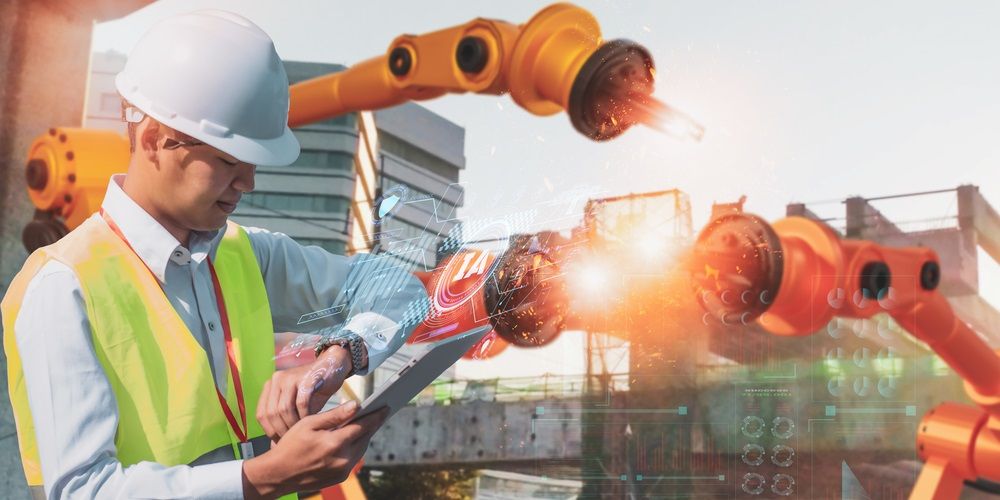
Moreover, preventive maintenance heavily relies on the assumption that increased machine use results in higher chances of breakdown. Under this approach, machines are discarded prematurely or replaced unnecessarily.
But research from the ARC Advisory Group shows that only 18% of industrial assets depreciate linearly with age.
Safer Work Environment
IoT predictive maintenance allows operation managers to foresee dangerous work conditions before they create any life threatening risk. For example, you will be able to predict surges in machine temperature or voltage and mitigate them to avoid fire hazards in the workplace.
Evaluation of Repairs
When a machine shuts down and repairs are made, predictive maintenance ensures that the repair was successful before you fire up the machine again. This prevents another shutdown to make extra repairs that you might have missed during the first shutdown.
Predictive maintenance systems are also effective at conducting several analyses. Using IoT sensors, the system can self-diagnose parameters such as vibration, temperature, and fluid levels, among others, before work resumes.
Lower Risk for Machine Failures
A functional predictive maintenance system normally eliminates the possibility of machine failure by 55%. With regular and preemptive checkups, equipment remains operational along any stage of the production process.
Short Lasting Repairs
In case of breakdown, there’s a likelihood that a repair will be conducted in a shorter time than when the failure was not anticipated. Constant monitoring of machine conditions provides a basis to understand a mechanical failure if it is inevitable.
In a survey of 500 plants, repair times before a predictive maintenance program were recorded and compared to those after one year of adopting the program. Researchers observed a 60% improvement in the mean time to repair (MTTR) after the program.
Predictive maintenance reduces the actual time required to repair or recondition plant equipment. You can reduce the mean time to repair (MTTR) by 60%.
To determine the average improvement, the actual repair times before the predictive maintenance program are compared to the repair time after one year of operation using predictive maintenance management techniques.
Increased Return on Investment (ROI)
When mechanical failures are identified in time, manufacturers tend to spend less on maintenance and repair. In addition to that, there is improved productivity when line workers and managers are focusing on core operations.
As a result of the reduced downtime and enhanced productivity, companies realise more return on investment on their assets.
Better Stock Management of Spare Parts
Predictive maintenance has the power to forecast the cost of repair, including labour, hardware, and other overheads.
During the repair, there are costs associated with purchasing and stocking of spare parts. Other than stocking all spare parts for machine repair at once, predictive maintenance ensures that you only stock replacement parts at the right time.
This decreases the cost of stocking by 30%.
Increased Revenue
When assets are protected from undue breakdowns, production schedules are fulfilled. In addition to increased productivity, short repair times and higher production quotas improve a company’s revenue streams from production.
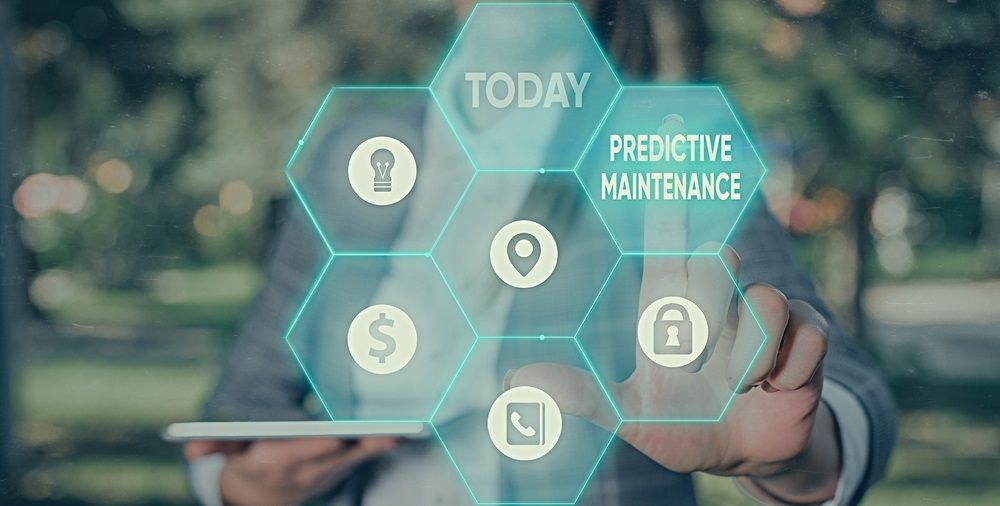
Applying IoT Predictive Maintenance
When you are starting out with IoT predictive maintenance, it’s important to start on a small scale. Consider testing the system on one asset in order to have an idea of how it fits within your business structure.
With time, you can decide the best approach to fully integrate your equipment with the technology.
Secondly, merge your software and predictive maintenance tools and collect performance data of your asset. The data is collected through sensors and then transmitted wirelessly to a cloud-based, centralized data storage platform in real-time.
Through machine learning and algorithms, the system will gather data about your asset’s condition. Your maintenance team will analyze this data and use it to predict when a failure might occur.
As you familiarize yourself with the dynamics of your pilot project, you can decide whether the predictive maintenance system is right for your model. If you are comfortable with the results, you may expand the system to other assets of your business.
As you scale up to an enterprise-wide predictive maintenance system, you will need a hand to take care of the technical bits so you can focus on your business strategy. IoT platforms like Ubidots make sure this process is as seamless and easy as possible.
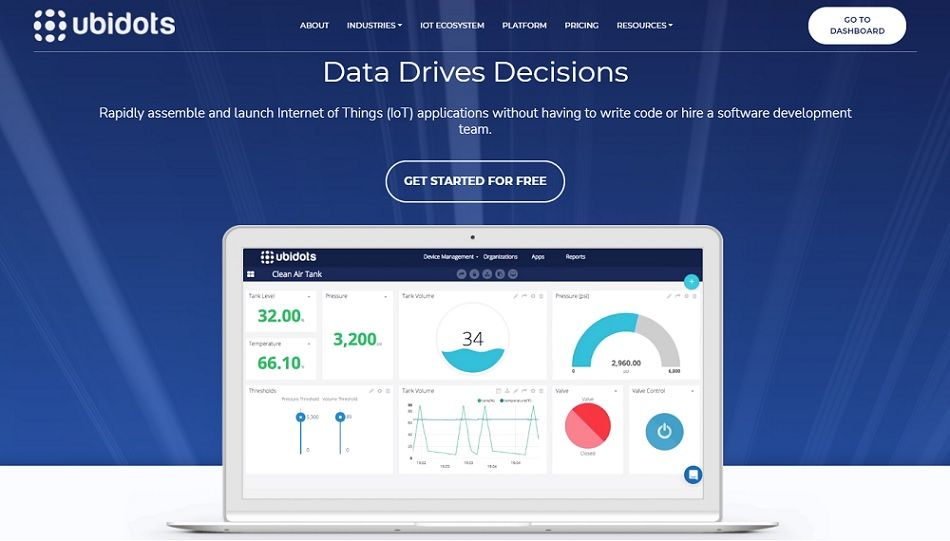
Conclusion
Predictive maintenance brings a high level of efficiency to how you use your assets. It saves you from unnecessary machine failure by predicting when a breakdown will occur.
The technology does this by using sensors to gather real-time data about your machine’s condition and creating performance reports that identify potential maintenance issues.
Predictive maintenance comes with a range of benefits, including reduced costs, higher profitability, less production downtime, and longevity of your machinery.
When implementing an IoT predictive maintenance system, it’s important to start small and then scale up when you understand how the technology fits in your production model.
We understand that starting new things is not always easy. In every step of the way, having the right information can be the difference between success and failure.
This is why Ubidots focuses on solving problems using data driven methods. Our experience in cloud-based applications has been refined over the years to create a robust engine of modern day problem solving.
Originally published 21 Dec 2021
Frequently Asked Questions
What are the three predictive maintenance benefits?
Low maintenance costs, improve utilization of machines and safer work environment.
What is predictive maintenance technology?
Predictive maintenance is the process of maintaining a system by predicting a fault in it before it happens.
How is IIoT used for predictive maintenance of machines in the industry?
IoT uses sensors to gather real-time data about your machine’s condition. It uploads the data wirelessly to a cloud where your maintenance team can access it 24/7 to create performance reports.