Cloud based SCADA: A Key Enabler for Industry 4.0 and IoT Adoption
Cloud-based SCADA systems extend the visualization of data beyond plant walls. Instead of being restricted to local networks, operators can access dashboards from anywhere. Thanks to their enhanced performance, dashboards become more dynamic, responsive, and customizable.
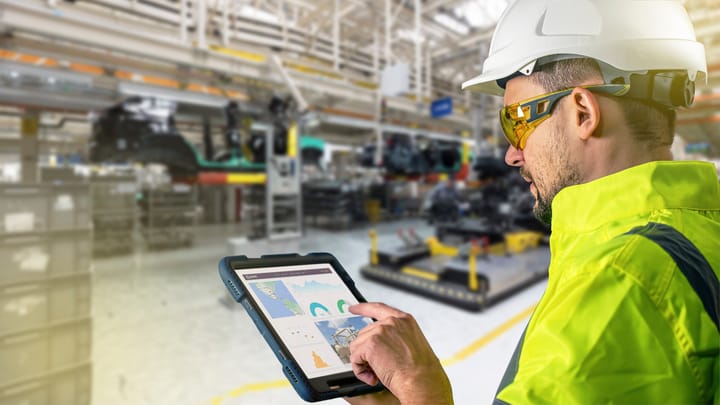
In a world where every second of downtime chips away at your plant’s bottom line, can you afford to stick with outdated control systems? Traditional SCADA systems have served their purpose, but the demands of modern manufacturing have outgrown them. Enter cloud-based SCADA systems—an agile, scalable, and cost-effective addition that’s not just an upgrade, but a transformation. Imagine having real-time monitoring of your operations from anywhere, using just a smartphone. A cloud based scada system provides real-time insights, helping organizations reduce operational costs, improve safety, and enhance efficiency. A SCADA in the cloud isn’t just a technological leap; it’s the key to unlocking the full potential of your plant’s Industry 4.0 ambitions. Ready to future-proof your operations? Let’s dive in.
Introduction
The Industrial Shift: Why Digital Transformation is Non-Negotiable
Digital transformation and Industry 4.0 are no longer just buzzwords—they are the keys for staying competitive. Failure to embrace them isn’t just a missed opportunity; it’s a threat to operational efficiency, profitability, and market relevance.
The Industrial Internet of Things (IIoT) has paved the way for smart manufacturing, where machines are interconnected, data flows seamlessly, and decisions are made based on real-time monitoring. But for all the benefits of IIoT, traditional SCADA systems are struggling to keep up. They lack the scalability in SCADA, flexibility, and data integration capabilities required in the digital age. As manufacturers push for leaner operations, faster decision-making, and enhanced productivity, cloud-based SCADA solutions have emerged as a critical enabler.
The Evolution of SCADA
SCADA: The Backbone of Industrial Control for Decades
For decades, Supervisory Control and Data Acquisition (SCADA) systems have been the beating heart of industrial operations. SCADA systems have provided reliability managers with an unparalleled level of oversight, enabling real-time monitoring and control of critical processes. From power grids to manufacturing plants, SCADA has acted as the silent enabler of efficiency, ensuring that machines hum along, alarms are triggered when something goes awry, and data is logged for future analysis.
These systems were revolutionary at their inception. They centralized control, reduced manual intervention, and gave managers a way to streamline operations like never before. Operators could sit in a control room and oversee entire plants, making SCADA a must-have for any serious industrial operation. For its time, SCADA was cutting-edge. It transformed how industries operated, bringing a new level of precision and control that had never been seen before.
The Limitations of Traditional SCADA in Today’s Manufacturing
But times have changed. What was once cutting-edge now feels like a bottleneck. Traditional SCADA systems, built on legacy SCADA architecture, are struggling to keep pace with the demands of modern manufacturing. These systems are often confined to on-premise SCADA hardware, limiting scalability and requiring costly maintenance. They lack the flexibility in SCADA systems to adapt to an environment where everything—from sensors to machines—is connected and data-driven.
The rise of IIoT, big data in SCADA, and cloud computing in manufacturing has exposed the limitations of traditional SCADA: Remote access is cumbersome, real-time data analysis is limited, and system upgrades can be both disruptive and expensive. Not to mention, traditional SCADA systems are often siloed, making it difficult to integrate with other technologies that are critical to digital transformation, such as artificial intelligence (AI) or machine learning in SCADA.
Industrial control has evolved. It’s time for SCADA to evolve with it.
The Emergence of Cloud-based SCADA
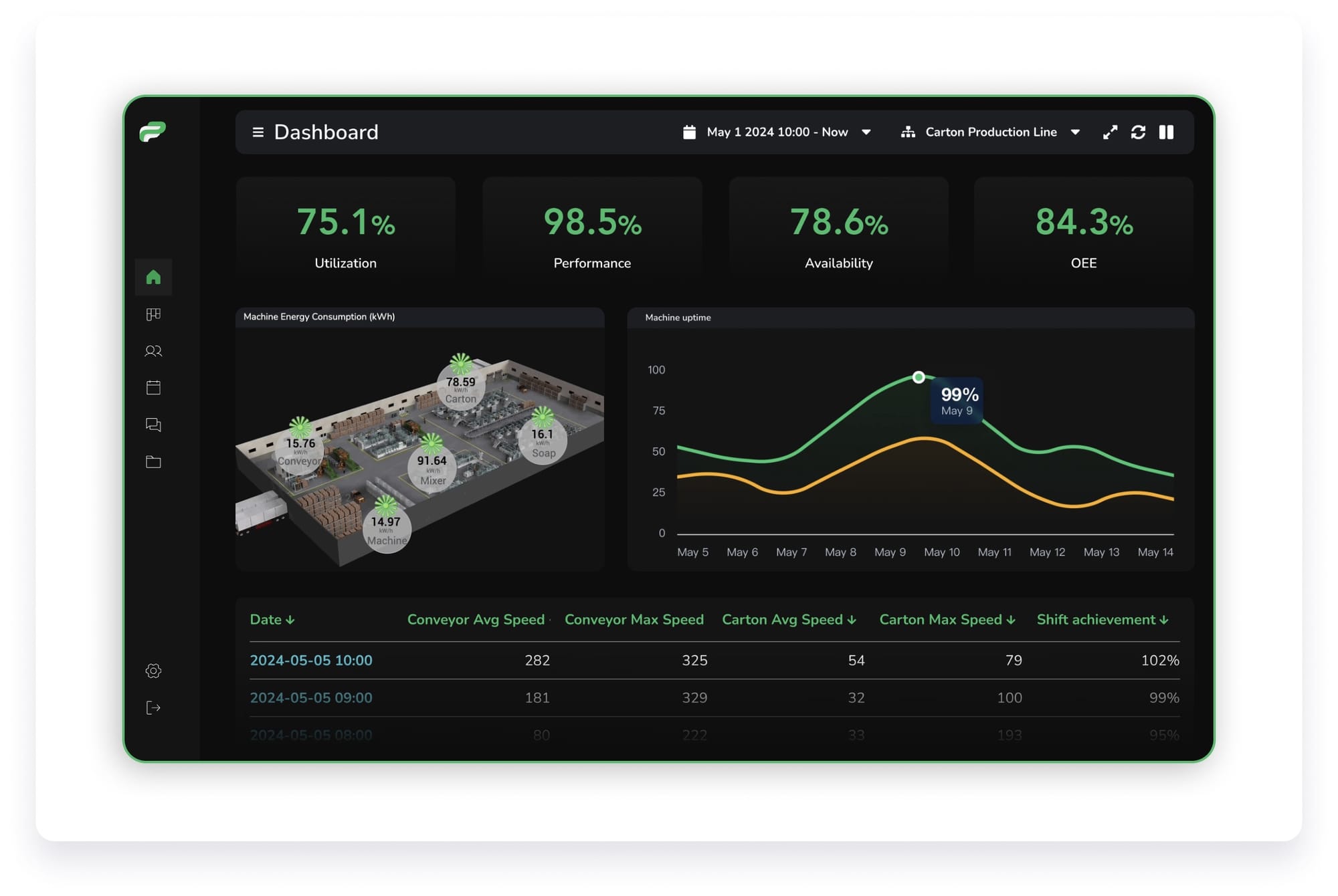
To understand how SCADA has evolved, it’s essential to grasp its layered SCADA architecture.
What are the four levels of SCADA?
SCADA systems traditionally operate on four distinct levels:
- Field Level: This is where the sensors, actuators, and machinery reside. These devices gather real-time data from the physical processes being monitored.
- Control Level: Programmable Logic Controllers (PLCs) and Remote Terminal Units (RTUs) operate here. These devices process data from the field, execute control actions, and relay information upward.
- Supervisory Level: This is the Human-Machine Interface (HMI) layer, where operators interact with the system. At this level, control rooms visualize the real-time data, allowing human supervisors to make critical decisions.
- Data Acquisition and Management Level: The highest level, where data is collected, stored, and processed for reporting and analysis. Traditional SCADA systems often rely on local servers for data acquisition, limiting scalability and remote access.
While these four levels have served industries well for decades, they are starting to feel the strain of modern industrial demands, particularly when it comes to scalability in SCADA and flexibility.
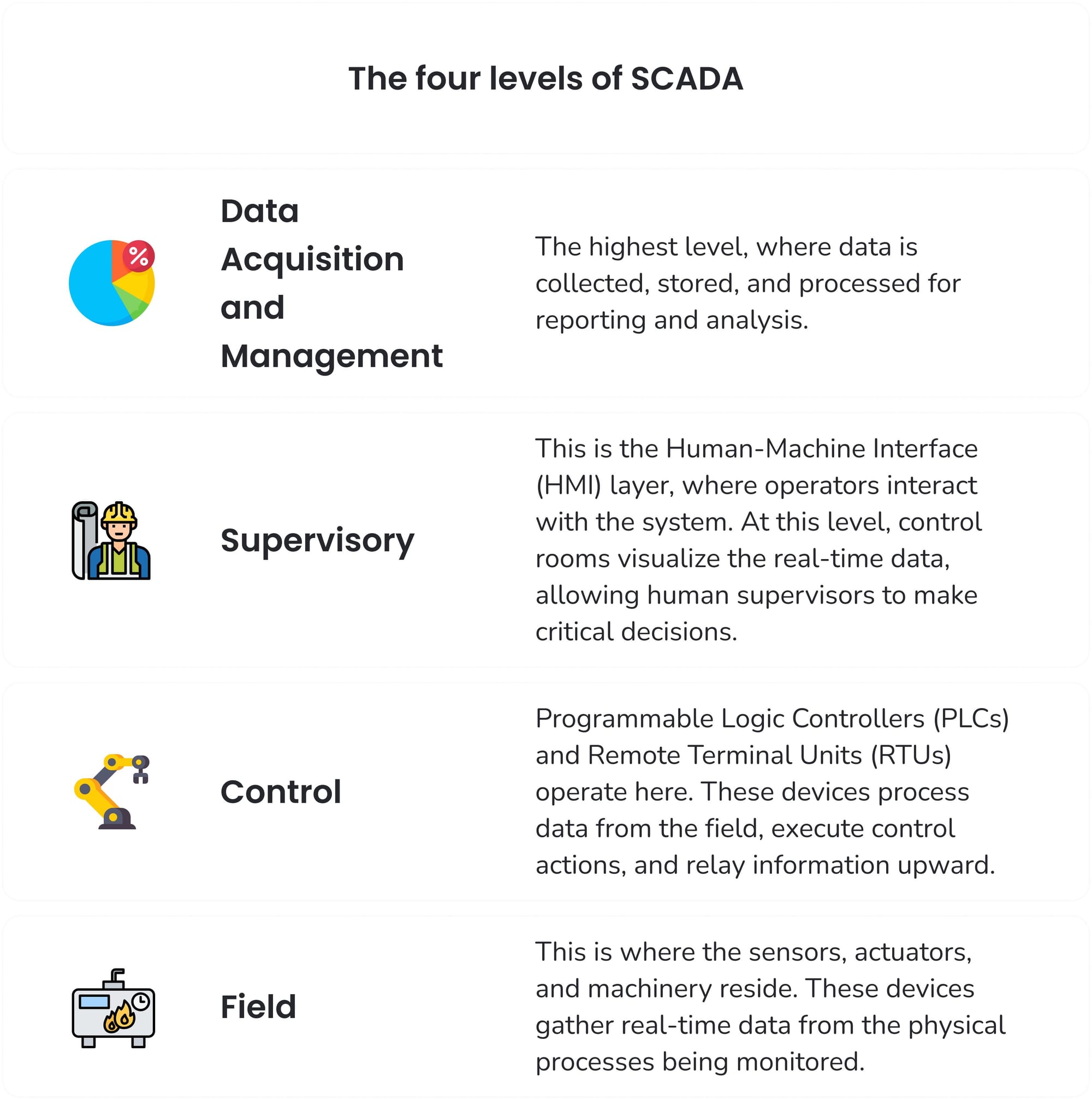
What are Cloud-based SCADA Systems?
Cloud-based SCADA builds upon the foundation of traditional SCADA without replacing it. Think of it as an extension that amplifies the capabilities of your existing SCADA infrastructure. At its core, it integrates with the fourth layer—Data Acquisition—shifting storage and real-time processing from local servers to the cloud. Cloud services offer significant advantages in improving efficiency and productivity for industrial operations, but they also come with challenges such as network availability and performance risks.
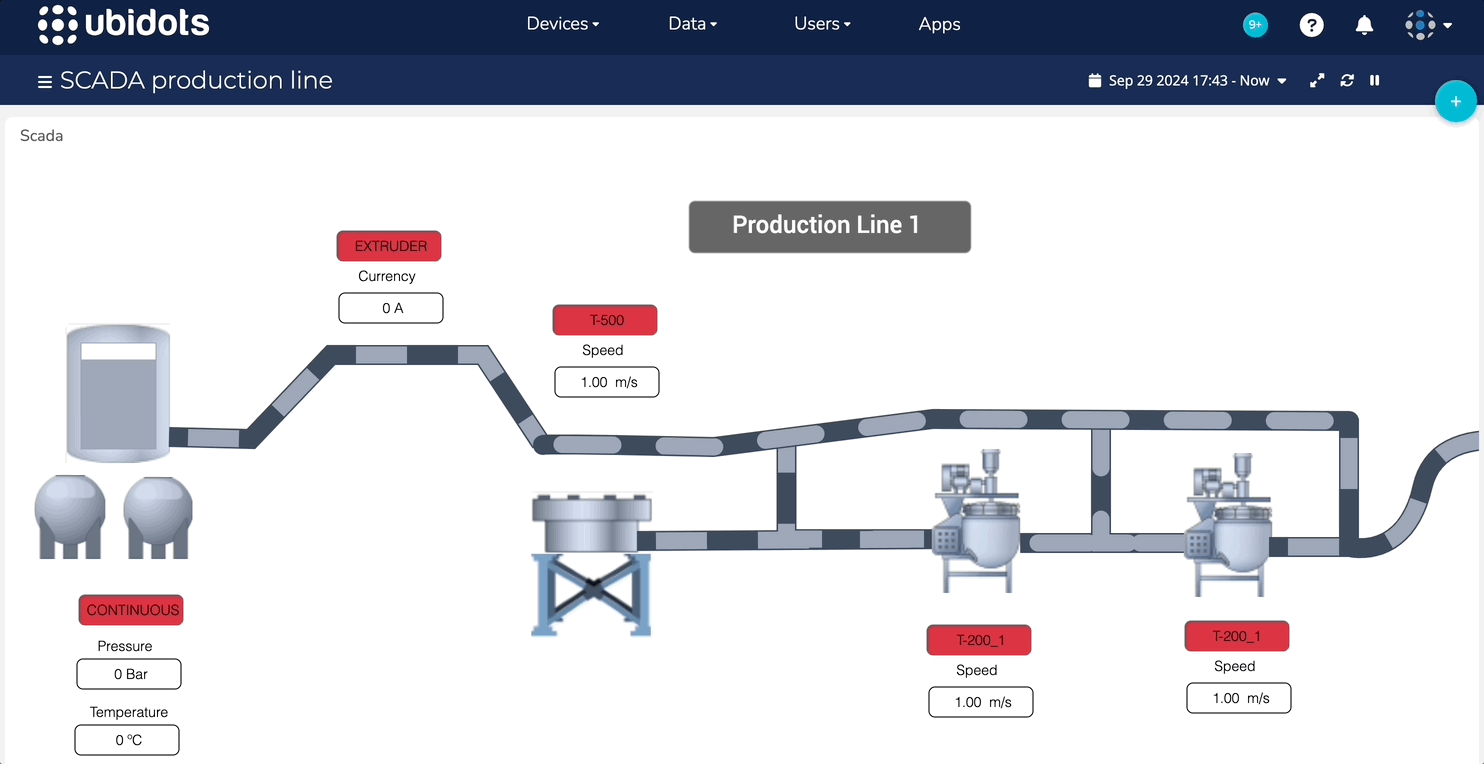
By connecting SCADA systems to the cloud, businesses can extend the visualization of data (traditionally done through HMIs) beyond plant walls. Industrial IoT gateways are crucial in facilitating these connections, ensuring seamless data flow between devices and the cloud. Instead of being restricted to local networks, operators can access dashboards from anywhere with an internet connection. This offers not just the same functionalities but also enhanced performance, thanks to the power of modern web libraries and real-time data processing tools, making dashboards more dynamic, responsive, and customizable.
Why is Cloud SCADA gaining popularity in Industrial Automation?
- Cost Efficiency: While a Cloud SCADA doesn’t completely eliminate the need for on-premise SCADA servers or hardware upgrades, it dramatically reduces the scope and cost of those investments. Traditional SCADA infrastructure will still handle critical local operations. But modifications to the system can be faster, more affordable, and less labor-intensive. Additionally, as web-based visualizations enter the factory floor, expensive, proprietary HMIs can be replaced with industrial PC screens running web browsers for non-critical processes. This shift allows businesses to leverage modern, flexible user interfaces without the need for costly, specialized hardware.
- Remote Access: One of the greatest advantages is the ability to access systems from anywhere with an internet connection. As a cloud solution, it can provide remote access while addressing security considerations (more on this below). Maintenance managers no longer need to be tied to the control room; with real-time data available on smartphones or tablets, issues can be diagnosed and addressed from halfway across the world, minimizing downtime and enhancing operational agility.
- Flexibility and Scalability: Traditional SCADA systems can struggle with scaling, often requiring costly and time-consuming hardware adjustments. Cloud-based SCADA, on the other hand, offers virtually unlimited scalability. As operations expand, adding new devices or scaling up data processing can be done with a few clicks, ensuring that the system grows alongside the business without bottlenecks.
- New Insights: With Cloud-based SCADA systems, businesses unlock new layers of industrial data analytics, but its true value lies beyond just analyzing existing PLC or Modbus data. By integrating an Internet-enabled data layer, companies can tap into an ever-expanding range of wireless IoT sensors, broadening the scope of what can be measured. This opens the door to new possibilities such as deploying smart weather stations to monitor pollution levels within factories, vibration sensors to predict machine failures, or environmental sensors for monitor workplace safety or process optimization. For a deeper dive into the types of sensors that could complement your system, check out these 12 IoT sensor types or these 5 Essential Modbus Sensors for Industrial Automation.
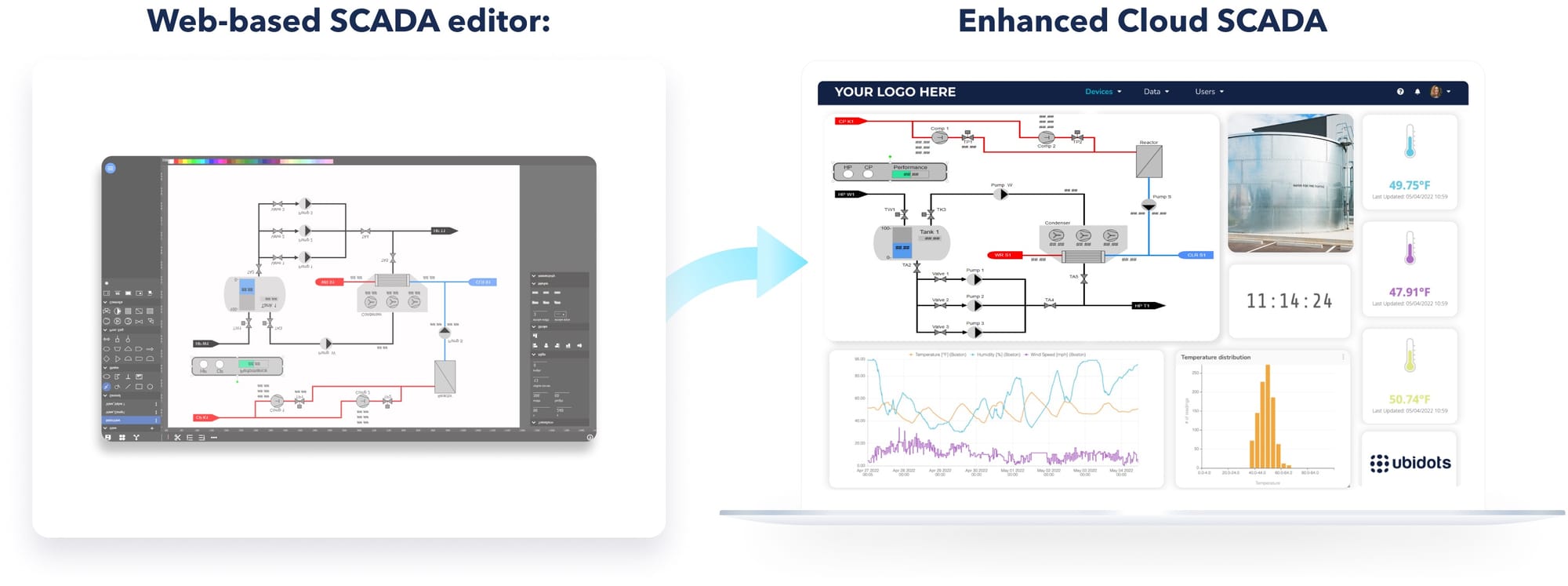
Cloud-based SCADA vs. Traditional SCADA: Key Differences
As industries embrace digital transformation, many wonder if Cloud SCADA is "better" than Traditional SCADA. But rather than acting as a replacement, Cloud SCADA serves as a powerful complement to traditional systems, enhancing their capabilities with remote monitoring, scalability, and advanced analytics. This side-by-side comparison explores the key differences between the two, helping you understand how they can work together to create more efficient, data-driven operations.
Topic | Traditional SCADA | Cloud-based SCADA |
---|---|---|
Cost Efficiency | - Requires large capital investments for hardware and upgrades. - Ongoing maintenance adds to operational costs. |
- Shifts costs to a more predictable, operational model. - Reduces need for frequent hardware overhauls and costly HMIs in non-critical areas. |
Remote Access | - Limited to local networks, often requiring Virtual Private Networks (VPNs) for external access. - Remote access setup is complex and expensive. |
- Accessible from anywhere with internet connectivity. - Streamlines remote monitoring without the need for VPNs or special configurations. |
Flexibility | - Requires significant manual interventions for system changes. - Hardware and software updates are time-consuming and disruptive. |
- Easily adaptable and customizable through cloud-based updates. - Supports rapid deployment of changes with minimal downtime. |
Scalability | - Expansion requires new hardware, significant time, and resources. - Scaling often leads to performance issues and operational bottlenecks. |
- Virtually unlimited scalability with cloud infrastructure. - Easily accommodates new devices and sites as operations grow. |
Real-Time Monitoring | - Real-time data is limited to local servers and specific control rooms. - Access is slower and dependent on physical infrastructure. |
- Provides real-time data from multiple sites simultaneously. - Enables faster decision-making with immediate data processing and analysis. |
The Power of Remote Monitoring and Remote Access
As noted in the above table, Cloud-based SCADA’s ability to provide real-time monitoring, effective data collection, and data acquisition across multiple sites significantly enhances decision-making in industrial automation. By allowing managers to observe processes remotely, Cloud-based SCADA transforms traditional monitoring methods into a proactive, data-driven system that offers a wide array of operational benefits within smart manufacturing.
Condition-based Monitoring and Data Acquisition
Condition-based monitoring (CbM) shifts the maintenance paradigm from reactive to predictive, leveraging industrial IoT capabilities. Traditional maintenance schedules often result in either premature part replacements or unexpected breakdowns. With Cloud-based SCADA, real-time monitoring of equipment conditions—such as vibration levels, temperature fluctuations, and pressure thresholds—becomes more intuitive and accessible. When anomalies are detected, Cloud-based SCADA systems send instant alerts through secure communication protocols such as MQTT over TLS, allowing teams to respond before a minor issue becomes a costly failure. This approach reduces downtime, minimizes unnecessary maintenance, and extends the life of critical assets.
OEE Monitoring
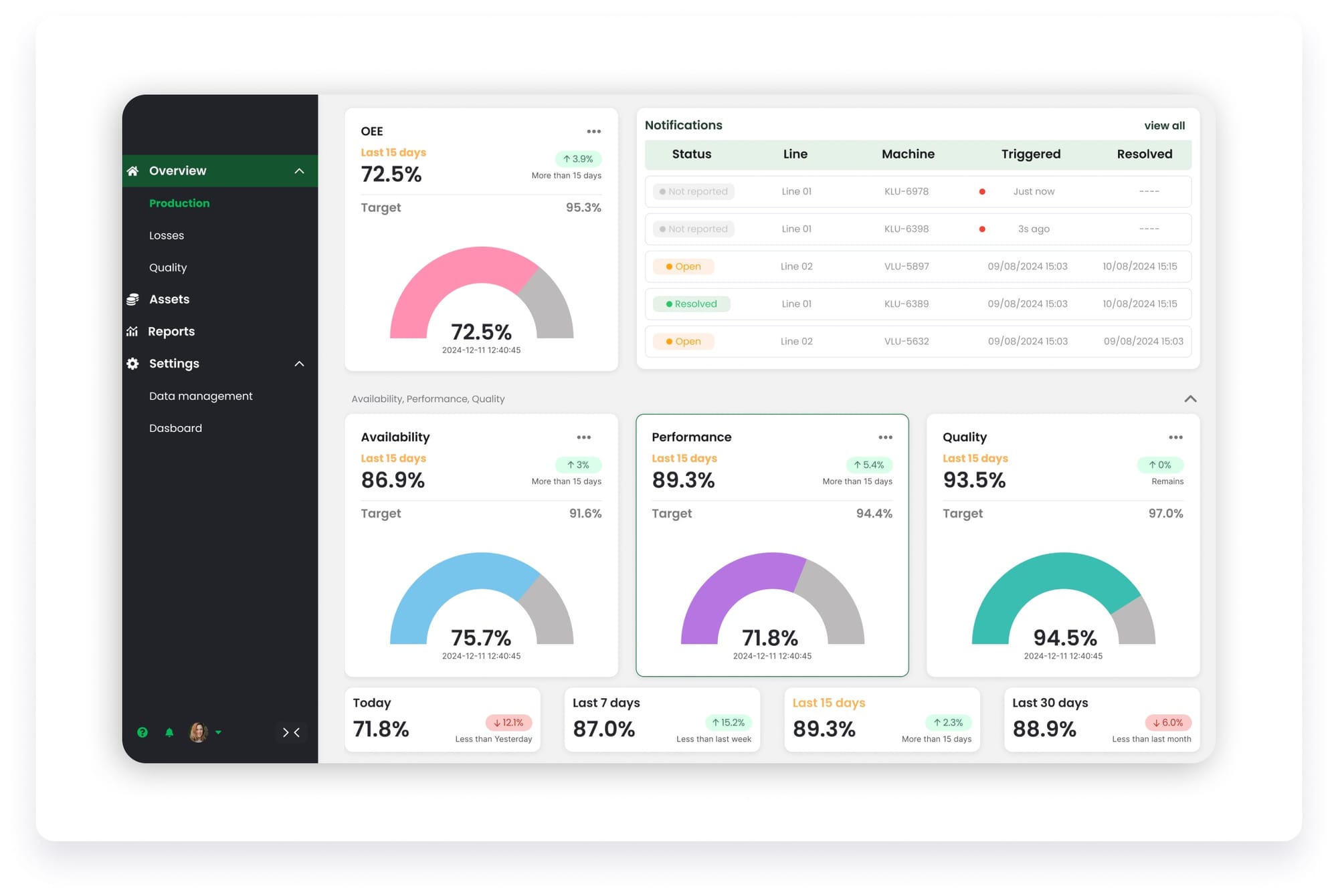
Measuring Overall Equipment Effectiveness (OEE) provides a clear snapshot of manufacturing efficiency, combining metrics of availability, performance, and quality into a single actionable figure. With traditional SCADA, gathering this data across multiple locations can be time-consuming and fragmented. A Cloud-based SCADA system simplifies the process by aggregating OEE data from various sites into one centralized platform through secure HMI integration. This not only allows for real-time data access but also enables swift adjustments to optimize productivity. By monitoring OEE remotely, operators can quickly identify performance bottlenecks and adjust operations on the fly, improving output and overall operational efficiency.
Energy Monitoring and Savings
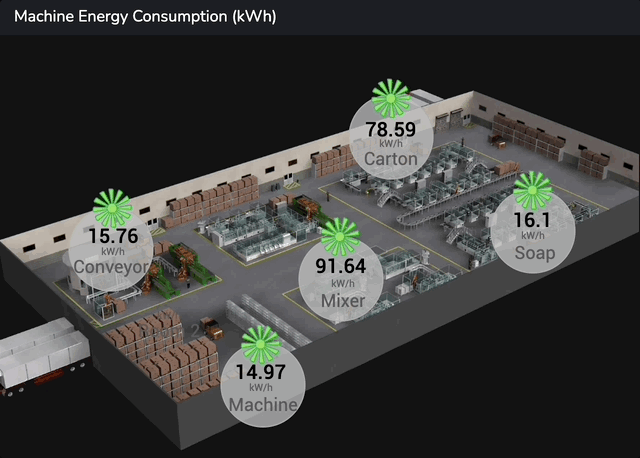
Energy consumption represents a major cost in any industrial facility, but inefficiencies are often difficult to track in real-time. Cloud SCADA’s energy management systems enable businesses to monitor energy usage with more granularity; from entire circuits down to the machine level. By identifying patterns of excess consumption or inefficiency, Cloud-based SCADA provides the insights needed to adjust operations, reducing energy waste and lowering overall costs. Whether shutting down equipment during idle times or scheduling energy-intensive processes during off-peak hours, real-time industrial data analytics on energy usage can drive both financial savings and sustainability efforts.
Addressing Security Concerns and Cyber Security
Cloud-based SCADA offers enormous benefits in terms of flexibility in SCADA systems and scalability, but it also introduces legitimate cyber security concerns, especially for IT departments. After all, connecting sensitive industrial systems to the cloud inherently opens up potential vulnerabilities. Ensuring that data security in SCADA is maintained is critical to gaining IT’s trust in these cloud-based solutions.
The Risk of Opening a Door to the Outside World
For IT professionals, extending a SCADA system to the cloud environment can feel like opening Pandora’s box. Historically, on-premise SCADA systems were siloed, kept behind a firewall with no external access. Introducing cloud-based SCADA applications changes this, creating fears of cyberattacks, data breaches, or unauthorized access to critical infrastructure. These concerns are heightened when dealing with operational technology (OT) systems, which traditionally aren’t designed with the same security layers as IT systems.
IT’s fears stem from legitimate concerns—critical processes could be interrupted, and sensitive data might be exposed. Many are wary of how secure communication between the cloud and on-premise infrastructure is handled, necessitating robust network security measures to safeguard cloud machines from external access.
Preventing Potential Vulnerabilities
Convincing IT teams that Cloud-based SCADA can be secure requires addressing these concerns with best practices designed to reduce vulnerabilities and protect critical industrial systems through effective security measures.
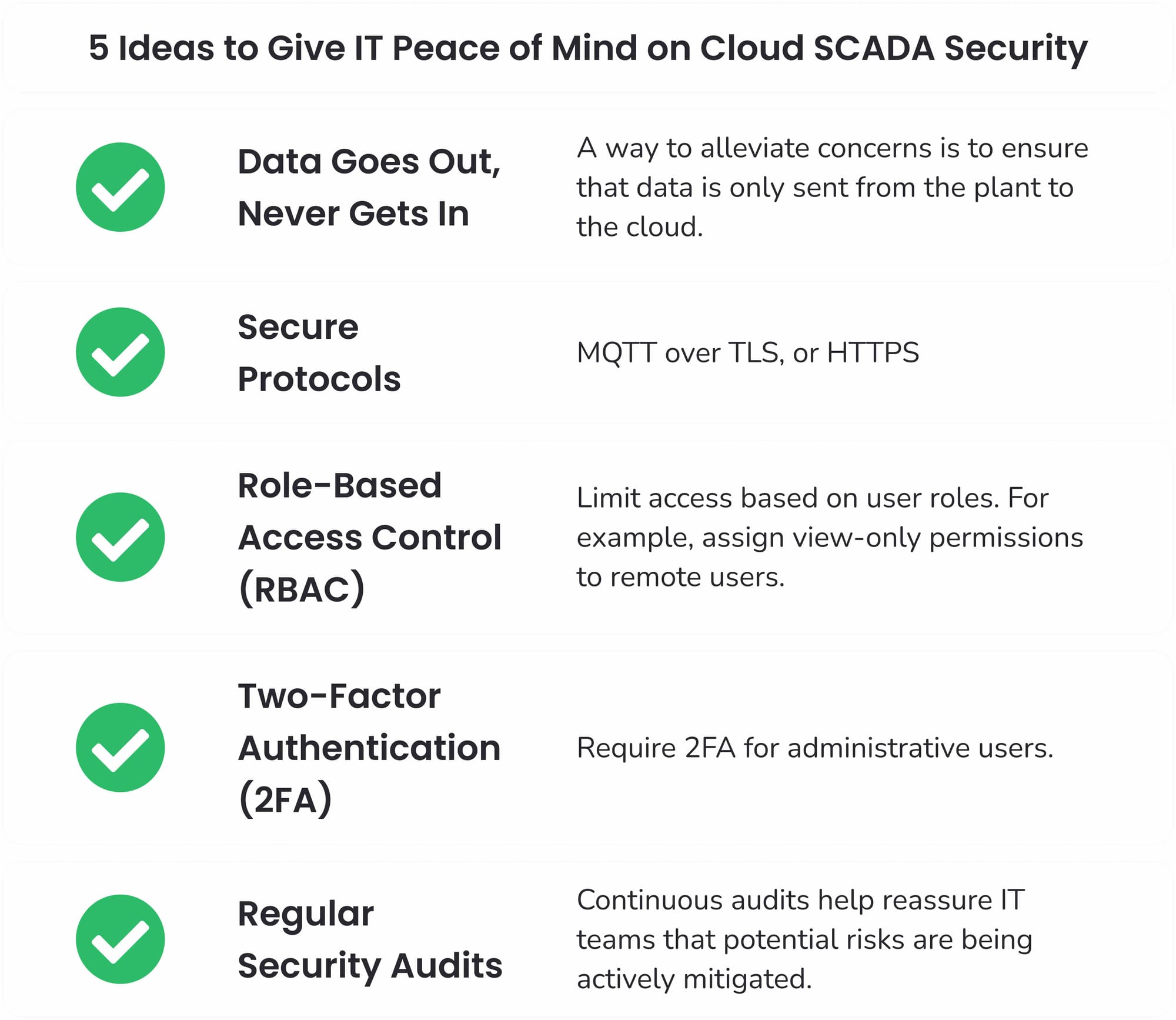
- Data Goes Out, Never Gets In: One way to alleviate concerns is to ensure that data is only sent from the plant to the cloud, preventing unauthorized external users from gaining control of internal systems. Cloud-based SCADA systems should be designed to allow outbound data flow only, ensuring internal systems remain isolated.
- Use Secure Protocols: Enforce data transport over secure communication channels like MQTT over TLS or HTTPS. These protocols ensure that all data transferred between the cloud and the local SCADA system is encrypted, preventing interception and unauthorized access during transmission.
- Role-Based Access Control (RBAC): Implement role-based access control systems that limit access based on user roles. For example, remote users can be assigned view-only permissions, ensuring they can monitor systems but not make critical changes, reducing the risk of human error or unauthorized actions.
- Two-Factor Authentication (2FA): Require 2FA for administrative users. This adds an extra layer of security, ensuring that even if login credentials are compromised, an additional authentication factor is required to access the system.
- Regular Security Audits: Propose regular security audits and vulnerability assessments of the cloud infrastructure. Continuous monitoring and improvements help reassure IT teams that potential risks are being actively mitigated.
By addressing these concerns head-on and incorporating strict secure SCADA communication protocols, you can demonstrate that a Cloud SCADA initiative is not only scalable and flexible but also secure.
Case Study: Real-World Success with Cloud SCADA
Prospect Control, an Australian company specializing in automation solutions, has embraced Cloud-based SCADA systems to modernize their clients’ operations, improve efficiency, and streamline industrial IoT integration. With clients across industries like mining, utilities, and manufacturing, Prospect Control needed to provide data collection and real-time monitoring solutions to ensure that their customers could optimize performance, reduce downtime, and enhance overall operational efficiency. Traditional SCADAs alone couldn't meet these modern demands, prompting them to adopt Ubidots Cloud-based SCADA system as a flexible and scalable solution.
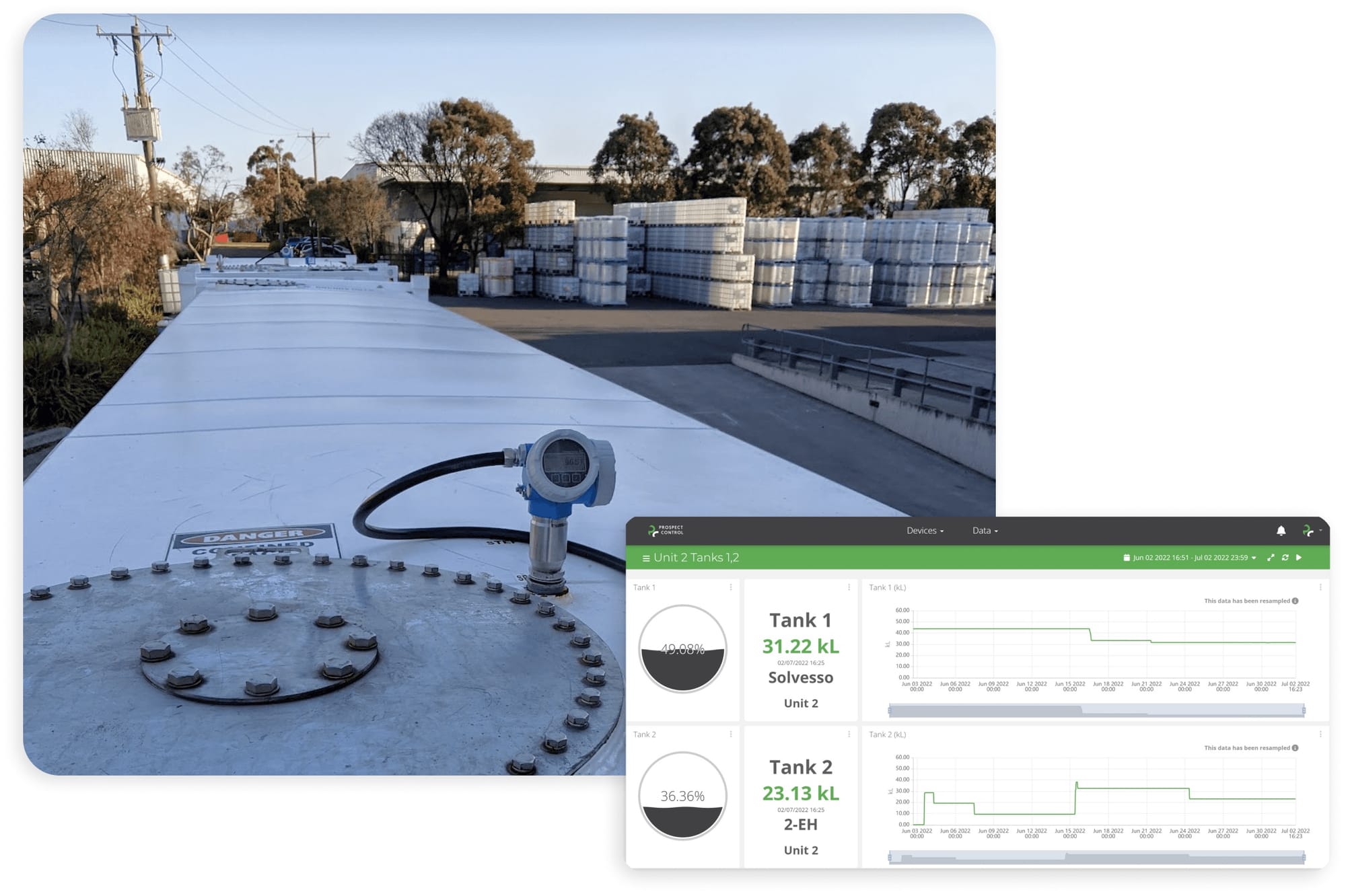
By leveraging Ubidots Cloud-based SCADA, Prospect Control seamlessly integrated real-time monitoring and control capabilities across their client base. This cloud-based platform allowed their clients to monitor critical parameters—such as equipment temperature, energy, and overall system performance—from any location, using intuitive dashboards accessible remotely. The adoption of Cloud-based SCADA significantly improved OEE monitoring for their clients, reducing downtime and enhancing production efficiency.
Additionally, this has enabled Prospect Control to introduce predictive maintenance strategies to their customers. Using data analytics and machine learning, the system could identify potential issues before they led to costly breakdowns, thereby reducing unplanned downtime. The result was not only a more streamlined production process but also improved energy management systems, allowing clients to monitor and reduce excess energy consumption, contributing to both cost savings and sustainability goals.
Prospect Control's clients have seen a marked improvement in operational efficiency, enhanced data security in SCADA, and reduced operational costs. This case study showcases the practical benefits of cloud-based SCADA solutions for industrial companies looking to stay competitive in an increasingly connected world.
Future Trends: Cloud SCADA, AI and Edge Computing
Cloud-based SCADA is rapidly evolving, and as the landscape of smart manufacturing continues to change, so do the capabilities of this powerful technology. With the integration of artificial intelligence (AI), machine learning (ML), and edge computing, Cloud SCADA is pushing the boundaries of what is possible.
- AI and machine learning are revolutionizing how data is processed and utilized in industrial IoT settings. Traditionally, SCADA systems were designed to monitor, control, and report data from various machines. Now, with AI and ML, Cloud-based SCADA is evolving from a purely reactive system to a predictive nature. By integrating AI algorithms, such as Anomaly Detection, Cloud SCADA can identify patterns in massive data sets that would be impossible for humans to detect. These insights enable predictive maintenance strategies, where ML models can anticipate equipment failures before they happen. This reduces downtime, optimizes machine performance, and extends the life of assets.
- Edge Computing brings computation and data storage closer to the physical location of devices, allowing for faster data processing and reduced latency. This is especially beneficial for operations that require real-time control and analysis. The integration with edge computing enables a hybrid system that combines the best of both worlds. Critical processes that demand immediate response can be handled locally at the edge, while cloud-based systems manage higher-level data processing, historical analysis, and predictive modeling. This hybrid approach ensures that operations remain resilient, even if connectivity to the cloud is temporarily lost.
As industries continue to embrace the combination of Cloud SCADA, AI, and edge computing, the future of smart manufacturing looks more dynamic and data-driven than ever. Manufacturers that adopt these technologies will be better positioned to stay competitive, drive innovation, and maintain
Conclusion
Why Cloud SCADA is the Foundation of Your Digital Transformation Strategy
Cloud-based SCADA is not just a technological advancement; it is the cornerstone of a future-proof industrial operation. As we’ve explored, traditional SCADAs, while reliable, are limited in their ability to scale, adapt, and provide the real-time monitoring and insights required in today’s fast-evolving manufacturing landscape. Cloud-based SCADA steps in as a powerful complement, offering cost efficiency, remote accessibility, and the flexibility needed to support growth and innovation in Industry 4.0.
With it, your operations become more than just reactive—they become proactive. From condition-based monitoring that prevents equipment failures to OEE monitoring that optimizes productivity, Cloud SCADA turns data into actionable insights, streamlining processes in real time. The ability to monitor and control systems remotely means that production never stops, even when you’re not on site, and predictive maintenance powered by artificial intelligence and machine learning reduces costly downtime.
Moreover, the integration of edge computing ensures that critical operations remain secure and efficient, even when cloud connectivity is limited. The combination of cloud and edge capabilities empowers manufacturers to make smarter, faster decisions with minimal latency, unlocking a new era of smart manufacturing.
In the end, digital transformation isn’t just about adopting new tools—it’s about future-proofing your business. By embracing Cloud SCADA, you’re not only optimizing today's operations but preparing for the challenges and opportunities of tomorrow.
FAQs
What is SCADA?
SCADA, or Supervisory Control and Data Acquisition, is a system used to monitor and control industrial processes. It gathers data from sensors and machines, processes that data, and provides operators with visual representations, allowing them to manage and optimize operations. SCADA is the backbone of industries like manufacturing, energy, and water treatment, where real-time monitoring and control are critical.
What is Cloud SCADA?
Cloud SCADA extends traditional a SCADA system by moving data storage, processing, and visualization to the cloud. This allows for enhanced scalability, remote monitoring, and data access from any location. Unlike traditional SCADA, which relies heavily on local servers and hardware, Cloud-based SCADA uses web-based tools to provide advanced features like predictive analytics and machine learning, complementing the existing SCADA infrastructure without replacing it.
Is Cloud SCADA a replacement for traditional SCADA systems?
No, Cloud SCADA is not a replacement but an extension of traditional SCADA systems. Traditional SCADA remains critical for handling local control, real-time responses, and system reliability. Cloud SCADA builds on this by enabling remote access, scalability, and advanced data analytics. Together, they create a more flexible and powerful infrastructure that supports digital transformation without compromising on-site performance.
What are the four levels of SCADA?
A SCADA system is typically structured into four layers:
- Field Level (Sensors and Actuators): Where data is gathered directly from machinery and equipment.
- Control Level (PLC/RTU): Programmable Logic Controllers and Remote Terminal Units process data and execute commands.
- Supervision Level (HMI): The Human-Machine Interface allows operators to visualize and interact with the system.
- Data Acquisition Level (SCADA Software): Data is collected and stored for analysis, traditionally using local servers but now increasingly processed in the cloud through Cloud SCADA for greater scalability and remote access.
This layered architecture ensures that operations remain efficient, secure, and adaptable to modern industrial needs.